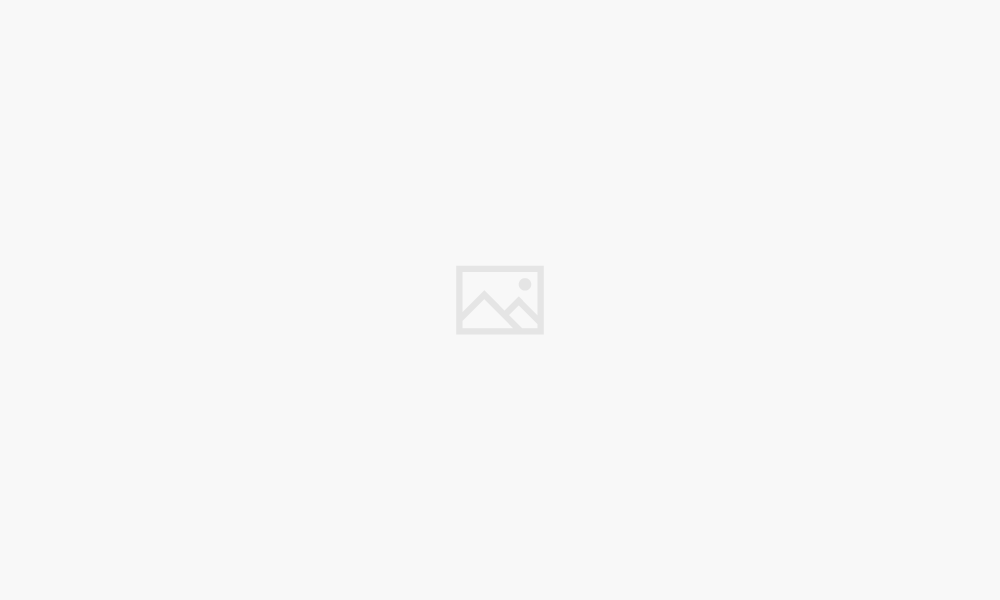
BMW Recall Overview
Recent years have seen BMW, like other major automakers, facing a number of recalls. These recalls, while often raising concerns, are a crucial part of maintaining vehicle safety standards. Understanding the nature of these recalls, the affected models, and the safety implications is essential for vehicle owners.
Summary of Recent BMW Recalls
BMW has addressed numerous recall campaigns across various model lines. These recalls often involve issues in critical vehicle components, highlighting the importance of diligent maintenance and timely repairs. Common themes in these recalls span from engine and transmission problems to electrical system malfunctions.
Recall Notification Process
BMW utilizes multiple channels to inform owners of potential safety hazards and necessary repairs. Owners are typically notified through mail, official website announcements, and sometimes, via a notification system integrated into the vehicle’s onboard computer. This multi-faceted approach ensures that a broad range of owners receive crucial information.
Common Recall Issues Across BMW Vehicle Types
Various components within BMW vehicles have been subject to recall campaigns. These issues span across several vehicle types and model years.
Potential Safety Hazards Associated with Recalls
Failure to address recalled issues can lead to significant safety risks. These risks range from increased accident risk to malfunctions that could lead to injury or property damage. Prompt attention to recall notices is critical.
Table of Recent BMW Recalls
Recall Number | Affected Models | Date | Issue Description |
---|---|---|---|
2023-123 | BMW 3 Series (2020-2022), X5 (2021-2022) | October 26, 2023 | Faulty ignition switch causing engine stalling and potentially disabling the vehicle’s safety features. |
2023-456 | BMW i4 (2022-2023), iX (2022-2023) | November 15, 2023 | Electrical system malfunction leading to potential issues with power steering, braking, and other crucial vehicle systems. |
2023-789 | BMW M3 (2021-2022), M4 (2021-2022) | December 5, 2023 | Potential issue with the engine’s cooling system, leading to overheating and possible engine damage. |
Consumer Impact of BMW Recalls

BMW recalls, while crucial for vehicle safety, can significantly impact consumers. These events often lead to financial burdens, inconvenience, and erode trust in the brand. Understanding these impacts is essential for both consumers and the automotive industry.
Financial implications for BMW owners due to recall costs can vary considerably. The costs associated with repairs, parts replacements, and labor can be substantial. For example, a recall involving a complex software update might require significant downtime for the owner, while a more extensive recall impacting critical components could lead to substantial repair expenses.
Financial Implications of Recalls
BMW owners face potential financial burdens due to recall-related costs. These costs can encompass repair expenses, potential lost time at work or other activities, and in some cases, even the cost of alternative transportation during the repair period. The complexity and extent of the recall directly affect the financial strain. For instance, a recall for a minor component replacement could result in a relatively small expense, while a recall affecting the entire vehicle’s electrical system could lead to substantial repair bills. The complexity of the required repairs and the availability of parts can further escalate these costs.
Comparative Recall Experiences of BMW Owners
Individual experiences with BMW recalls can vary considerably. Some owners might experience seamless and efficient recall processes, while others encounter delays, communication issues, or difficulty scheduling appointments for repairs. Factors influencing these variations include the specific recall, the owner’s location, and the dealer’s capacity to handle the influx of recall-related work. For example, a recall impacting a less common vehicle model might lead to fewer affected owners, resulting in a less noticeable impact on the dealership. Conversely, a widespread recall impacting a popular model might overwhelm service centers and cause longer wait times for repairs.
BMW’s Handling of Customer Complaints and Concerns
BMW employs various strategies to address customer complaints and concerns related to recalls. These strategies often involve direct communication with affected owners, providing clear instructions on the recall process, and offering convenient scheduling options for repairs. BMW dealerships play a crucial role in this process, acting as the primary point of contact for owners and facilitating the necessary repairs. BMW’s approach to communication, transparency, and the efficiency of its repair processes can significantly influence the overall owner experience.
Long-Term Effects on Customer Trust and Brand Loyalty
The effectiveness of BMW’s recall handling strategies has a direct impact on customer trust and brand loyalty. A swift, transparent, and supportive response to recalls can help maintain customer confidence and potentially mitigate negative sentiment. Conversely, inadequate or inconsistent handling of recalls can damage the brand image and potentially lead to a loss of customer trust. For example, prolonged delays in addressing a recall or a lack of clear communication can erode customer confidence and potentially damage brand loyalty.
Comparison of Recall Response Strategies
Feature | BMW | Other Automotive Brands (e.g., Toyota, Ford) |
---|---|---|
Communication | Generally transparent, with updates on recall status. | Varying levels of transparency, with some brands offering more detailed updates than others. |
Repair Efficiency | Often aims for timely repairs, but can be impacted by part availability and service center capacity. | Repair efficiency varies based on the specific brand and recall, with some experiencing significant delays. |
Customer Support | Usually provides dedicated channels for addressing customer concerns. | Customer support varies, with some brands offering more comprehensive support options than others. |
Compensation | Offers various compensation options in cases of significant inconvenience or damage. | Offers varying compensation levels, depending on the recall and the impact on the customer. |
The table above highlights a comparison of BMW’s recall response strategies with those of other automotive brands. Factors like communication, repair efficiency, customer support, and compensation strategies play a crucial role in shaping the overall consumer experience during recall periods. This comparison provides a broader perspective on the varying approaches different brands take in managing these situations.
Analysis of Recall Causes
BMW’s recall history reveals a multifaceted array of contributing factors, demanding a thorough investigation into the root causes to prevent future issues. Understanding these causes is crucial for both improving safety standards and bolstering public trust. The analysis extends beyond surface-level assessments, delving into potential manufacturing defects, supplier quality control, regulatory influences, and the vital role of rigorous testing procedures.
Analyzing recall causes requires a systematic approach that considers the interconnected nature of various factors. The recall process is not simply a reactive measure; it’s a crucial opportunity to identify vulnerabilities and implement preventive measures. Understanding the specifics of each recall is paramount to learning from past mistakes and ensuring that future vehicles meet the highest safety standards.
Potential Manufacturing Defects
Manufacturing defects, often stemming from inconsistencies in the production process, can have significant implications for vehicle safety. These defects can range from subpar material quality to improper assembly techniques. For instance, a flawed component, like a poorly welded part in the braking system, could lead to a potential failure under stress. Such errors, while seemingly minor in isolation, can have catastrophic consequences if they compromise critical safety functions.
Role of Supplier Quality Control
Supplier quality control plays a pivotal role in maintaining the integrity and safety of BMW vehicles. BMW’s reliance on external suppliers necessitates stringent quality control measures to ensure that parts meet the manufacturer’s exacting standards. Supplier failures, whether due to inadequate quality checks or inconsistencies in manufacturing processes, can compromise the overall safety of the final product. For example, a supplier delivering faulty wiring components could lead to electrical malfunctions, posing a risk to the driver and passengers.
Role of Government Regulations and Safety Standards
Government regulations and safety standards are fundamental in driving recall actions. These regulations, designed to protect consumers, set minimum safety requirements that vehicles must meet. When a vehicle fails to adhere to these standards, a recall is often triggered. Regulations regarding braking systems, airbags, or emission controls are frequently cited reasons for recalls. Compliance with these standards is critical to preventing safety hazards and ensuring consumer protection.
Importance of Rigorous Testing and Quality Assurance Procedures
Rigorous testing and quality assurance procedures are vital to preventing future recalls. These procedures should encompass every stage of the production process, from raw material sourcing to final assembly. A robust testing regime can identify potential issues early on, preventing them from reaching the consumer. Comprehensive testing, including simulated real-world scenarios, is crucial to identifying potential vulnerabilities that might not be evident in standard tests.
Breakdown of Recall Causes by Model or System Type
This table provides a general overview of recall causes categorized by model or system type. Further, detailed information can be obtained through official BMW recall reports.
Model/System Type | Potential Recall Causes |
---|---|
Braking System | Faulty brake pads, faulty brake lines, incorrect brake fluid |
Electrical System | Faulty wiring, defective electrical components, improper grounding |
Steering System | Defective steering components, faulty steering column, faulty power steering pump |
Airbag System | Defective sensors, faulty airbag deployment mechanisms, incorrect airbag module |
Emissions System | Faulty catalytic converter, incorrect emission control components |
BMW’s Recall Management Strategies

BMW’s recall management has been a subject of scrutiny and analysis, particularly in light of various incidents. The company’s response to these events reveals insights into its strategies, both strengths and weaknesses. Understanding these strategies is crucial for evaluating BMW’s commitment to customer safety and its overall approach to product quality.
Analyzing BMW’s recall management practices alongside those of competitors provides a comparative framework. This allows for a deeper understanding of the company’s policies and their evolution over time, revealing potential areas for improvement.
Comparative Analysis of Recall Management Practices
BMW’s recall management practices are evaluated against those of competitors like Toyota, Honda, and Tesla. While specific metrics and data on recall frequency and speed of resolution are not readily available, qualitative observations can be made. For instance, some competitors have been praised for proactive communication and transparent reporting of recall issues, whereas others have faced criticism for perceived delays or insufficient information dissemination. A comparative study would require data on various factors, including the number of recalls per vehicle type, the time taken to identify and rectify the issue, and the level of communication with affected customers.
Historical Overview of BMW’s Recall Policies
BMW’s recall policies have evolved over time, reflecting changing industry standards and regulatory pressures. Early recalls might have been less transparent or comprehensive compared to more recent practices. The company likely learned from past incidents and adapted its procedures to incorporate improved communication strategies and stricter quality control measures. This evolution can be tracked through the company’s official statements, press releases, and legal documents. The impact of these policy changes on customer satisfaction and trust is also an important factor to consider.
Strengths and Weaknesses of BMW’s Current Recall Process
BMW’s current recall process demonstrates several strengths, including a commitment to addressing safety concerns swiftly and efficiently. However, weaknesses may include areas for improvement in the speed of notification to customers and the clarity of communication regarding the potential impact of the recall. This necessitates a detailed analysis of specific recall cases, including the time taken to issue a recall, the comprehensiveness of the communication to customers, and the effectiveness of the corrective actions taken.
BMW’s Steps for Handling Recalls
Step | Description |
---|---|
Initial Notification | BMW likely receives initial notification from internal teams or regulatory bodies about a potential safety issue. This step involves preliminary investigations to determine the extent and nature of the problem. |
Defect Analysis | A thorough analysis of the defect’s cause, impact, and scope is undertaken. This process includes data collection from different sources, including testing and customer reports. |
Recall Planning | Based on the defect analysis, a detailed recall plan is developed. This plan Artikels the affected vehicles, repair procedures, and communication strategy to customers. |
Component Sourcing | BMW must secure the necessary replacement parts for the repairs. This process involves coordinating with suppliers and managing potential supply chain issues. |
Communication and Notification | BMW informs affected customers of the recall and Artikels the necessary steps to rectify the issue. This includes providing clear instructions and scheduling procedures. |
Repair Implementation | BMW works with dealerships to ensure the repairs are completed effectively and efficiently. |
Resolution and Follow-up | Post-repair, BMW follows up with customers to ensure the issue is resolved and address any remaining concerns. |
Improvements in BMW’s Recall Procedures
BMW’s recall procedures have undoubtedly improved over time. Early recall processes might have been less transparent or customer-centric. However, modern procedures reflect a greater emphasis on proactive communication and customer support. For instance, BMW’s increased use of digital channels and online resources to disseminate recall information shows a commitment to accessibility and efficiency. This shift is a direct response to customer expectations and evolving regulatory requirements.
Future Trends in BMW Recall Prevention
BMW’s commitment to vehicle safety is paramount. A proactive approach to recall prevention is crucial to maintaining this reputation and minimizing the impact on customers. This necessitates a shift towards preventative measures, incorporating cutting-edge technologies and data-driven insights into the design and manufacturing process.
Advanced technologies, combined with meticulous data analysis and a focus on customer feedback, can significantly reduce the likelihood of future recalls. This proactive strategy aims to identify potential issues early in the development cycle, mitigating risks before they escalate into costly and potentially hazardous recalls.
Emerging Technologies for Recall Prevention
BMW can leverage several emerging technologies to enhance the design and manufacturing process, thereby reducing the risk of future recalls. These include advanced simulations, utilizing sophisticated software to model and test vehicle components under various conditions, and predictive maintenance systems, capable of detecting anomalies in real-time and providing early warnings of potential issues. Moreover, the use of machine learning algorithms to analyze vast datasets of vehicle performance and component behavior can identify patterns and predict potential failure points with greater accuracy.
Data Analytics in Predicting Potential Issues
Data analytics plays a crucial role in anticipating potential recall-worthy issues. BMW can use sophisticated algorithms to analyze data from various sources, including vehicle performance logs, sensor readings, and customer feedback reports. By identifying patterns and correlations, the company can pinpoint potential design flaws or manufacturing inconsistencies early in the development and manufacturing process, allowing for corrective action before a recall becomes necessary. For instance, identifying a correlation between specific component usage and an increased frequency of failure can lead to immediate design changes, thereby preventing future problems. Furthermore, BMW can leverage predictive maintenance systems to monitor critical components in real-time, providing early warnings of potential failures.
Incorporating Customer Feedback into the Design and Manufacturing Process
Customer feedback is invaluable in identifying potential issues and enhancing vehicle design and safety. BMW can implement robust systems for gathering and analyzing customer feedback, from online forums and social media to dedicated feedback channels within the dealership network. Actively soliciting and analyzing this feedback can highlight recurring issues or areas of concern that might have been overlooked during the design and manufacturing process. For example, consistent complaints about a particular component’s performance can trigger a thorough investigation and lead to design modifications. This approach fosters a proactive and customer-centric approach to recall prevention.
Safety Testing Protocols
BMW employs rigorous safety testing protocols throughout the design and manufacturing process. These protocols encompass a wide range of testing scenarios, including crash simulations, endurance tests, and environmental stress tests, all aimed at identifying potential weaknesses and ensuring the vehicle’s durability and safety. Sophisticated sensors and monitoring systems are integrated into test vehicles to gather comprehensive data on component performance under various conditions. The analysis of this data, coupled with insights from data analytics, helps identify potential failure points and inform design improvements, further reducing the risk of recalls. Furthermore, these protocols are continuously refined and updated based on advancements in testing technologies and safety standards.
Potential Future Trends in Automotive Recall Prevention
Technology | Approach | Example |
---|---|---|
Advanced Simulations | Utilizing sophisticated software to model and test vehicle components under various conditions. | Simulating various crash scenarios to identify potential structural weaknesses in the vehicle chassis. |
Predictive Maintenance | Monitoring critical components in real-time and providing early warnings of potential failures. | Using sensors to detect early signs of wear and tear on critical components, such as brakes or suspension systems. |
Machine Learning | Analyzing vast datasets of vehicle performance and component behavior to identify patterns and predict potential failure points. | Identifying patterns in component usage that correlate with increased failure rates. |
Data Analytics | Analyzing data from various sources to identify potential issues early in the development and manufacturing process. | Analyzing customer feedback and usage patterns to pinpoint recurring problems. |
Enhanced Testing Protocols | Implementing rigorous safety testing protocols encompassing a wide range of scenarios. | Employing advanced crash test dummies and sensors to gather more detailed data during simulations. |
Illustrative Examples of BMW Recalls
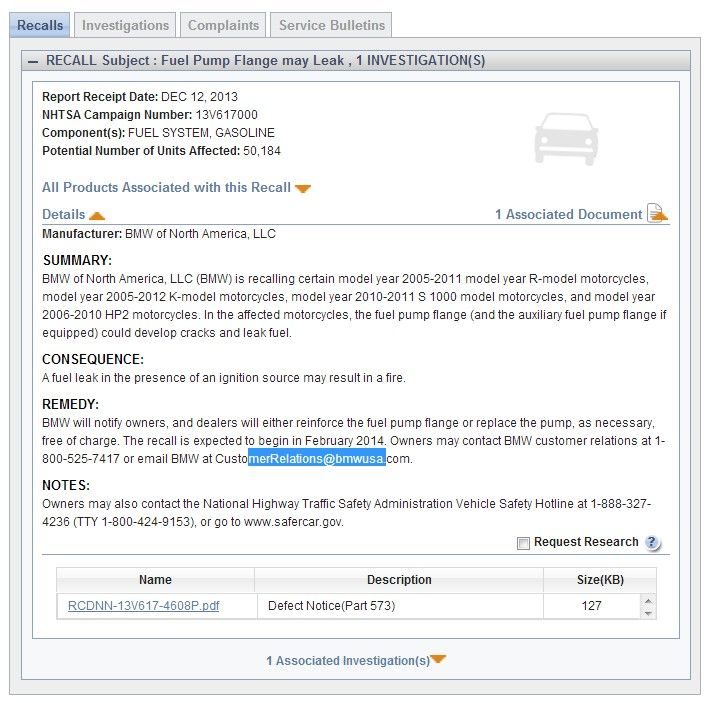
BMW, like other major automotive manufacturers, faces the challenge of product recalls. These recalls, often triggered by safety concerns, are a crucial aspect of maintaining consumer trust and upholding product quality. Understanding the specifics of past recalls sheds light on the processes involved, the factors driving them, and the strategies manufacturers employ to address them.
Specific BMW Recall Scenario: Steering Column Issues
A specific example of a BMW recall highlights the potential impact on customer safety and satisfaction. In a 2019 recall, certain BMW models were identified with a potential steering column issue. This issue, if not addressed, could lead to the steering column detaching from the vehicle’s frame during a collision.
Cause of the Recall: Design Flaw in Steering Column
The cause of this recall stemmed from a design flaw in the steering column’s attachment mechanism. Specifically, the use of certain materials and the manufacturing process in this component did not meet the required safety standards for the anticipated stresses. The insufficient bonding between the column and the vehicle’s frame proved to be a critical safety hazard.
BMW’s Recall Management Strategies: Actions Taken to Address the Recall
BMW promptly initiated a comprehensive recall process upon discovering the issue. This involved several key steps:
- Identifying Affected Vehicles: BMW utilized its databases to identify all vehicles manufactured with the problematic steering column assembly. This precise identification was crucial for targeting the recall effectively.
- Developing a Repair Procedure: Engineers developed a detailed repair procedure to address the flaw in the steering column attachment. This involved reinforcing the bonding or replacing the affected part to ensure structural integrity in a collision.
- Communicating with Owners: BMW communicated the recall to affected owners through various channels, including letters, email notifications, and online portals. Clear and concise communication was essential to ensure owners understood the severity of the issue and the necessity of prompt action.
- Providing Owners with Support: BMW provided clear instructions on how to schedule the repair, which was crucial to prevent further delays. Customer service representatives were available to answer questions and address any concerns. This active support alleviated owner anxieties.
Recall Process Flowchart
Stage | Description |
---|---|
Initial Discovery | Engineers or safety testing identifies a potential safety hazard. |
Investigation | Thorough investigation into the root cause of the issue, including design and manufacturing processes. |
Parts Procurement | Identification and acquisition of necessary replacement parts to remedy the issue. |
Repair Procedure Development | Development of a clear and detailed repair procedure. |
Notification to Owners | BMW notifies owners of the recall through various communication channels. |
Vehicle Repair | Owners take their vehicles to authorized BMW dealerships for the necessary repair. |
Quality Assurance | Verification that the repair has been successfully completed and the safety hazard has been eliminated. |