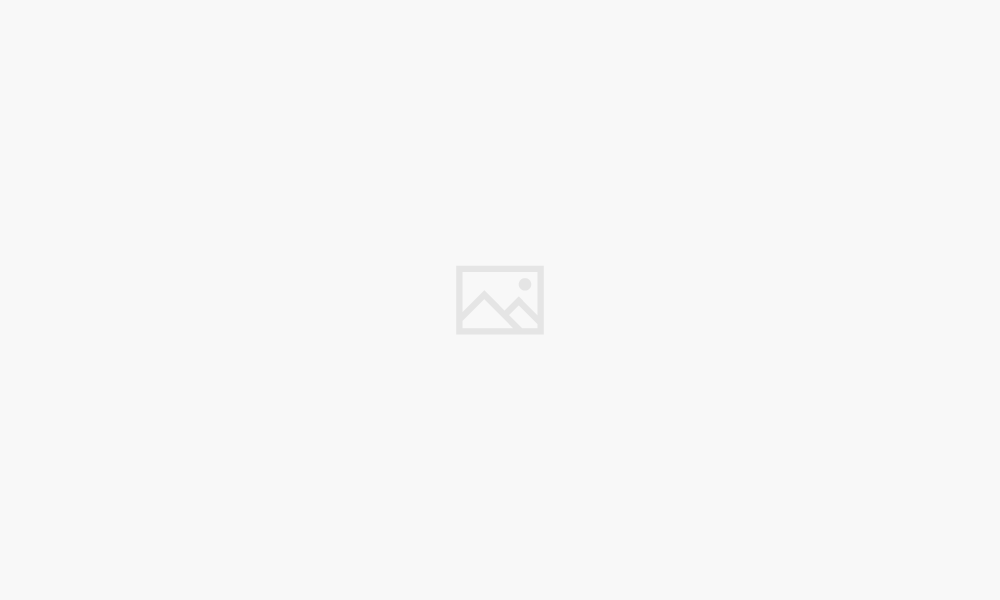
Job Market Trends
The automotive industry, a cornerstone of global economies, is undergoing a period of significant transformation. This shift is driven by evolving consumer preferences, technological advancements, and a renewed focus on sustainability. Understanding these trends is crucial for companies like Toyota, as they navigate the complexities of the modern job market and prepare for future opportunities.
The current state of the automotive job market is characterized by both challenges and opportunities. While traditional manufacturing roles remain important, a growing demand for skilled technicians and engineers capable of handling electric vehicle (EV) technology is evident. Toyota, a leader in hybrid technology, is at the forefront of this transition, facing the need to adapt its workforce to meet these changing requirements.
Current State of the Automotive Job Market
The automotive industry is experiencing a dynamic shift, marked by a rise in demand for specialized skills in areas such as electric vehicle (EV) engineering, software development, and battery management. This transition presents both opportunities and challenges for companies like Toyota. Companies need to invest in training programs and reskilling initiatives to equip their existing workforce with the necessary expertise to thrive in the evolving landscape. The increasing adoption of autonomous driving technologies is further complicating the skillset requirements, demanding professionals with expertise in artificial intelligence, machine learning, and sensor technology.
Future Projections for Employment Opportunities in Toyota’s Car Sector
Future employment opportunities in Toyota’s car sector will likely be heavily influenced by the increasing adoption of electric vehicles. Toyota’s existing expertise in hybrid technology will be crucial in this transition. As electric vehicles become more prevalent, roles in battery manufacturing, charging infrastructure development, and EV maintenance will emerge as significant opportunities. The development and implementation of advanced driver-assistance systems (ADAS) will also create a demand for skilled engineers and technicians specializing in software, sensor technology, and autonomous driving systems. Predictions suggest a continued need for experienced manufacturing personnel, although their roles will likely evolve to encompass the integration of new technologies into production processes.
Comparison of Automotive and Toyota-Specific Job Market Trends
While the automotive industry as a whole is experiencing a shift towards electrification and automation, Toyota’s specific job market trends are shaped by its unique position in the market. Toyota’s early embrace of hybrid technology provides a competitive edge, potentially leading to a higher demand for engineers and technicians with expertise in hybrid and electric vehicle systems. Toyota’s commitment to lean manufacturing principles, coupled with its focus on quality, will likely continue to influence the types of manufacturing roles available, although these roles may evolve to incorporate the demands of EV production. The need for skilled personnel in areas like battery management, charging infrastructure, and software development will be crucial for Toyota’s success in the future.
Potential Skills Gaps or Shortages in the Toyota Automotive Workforce
Toyota faces potential skill gaps and shortages in several key areas. The rapid advancement of EV technology presents a significant challenge, as the company needs to upskill its workforce in areas such as battery technology, electric motor design, and EV-specific software development. The demand for professionals with expertise in autonomous driving technologies and the associated software development and sensor integration is also expected to increase. Moreover, the company needs to cultivate a skilled workforce capable of handling the increased complexity of interconnected systems within future vehicles. A proactive approach to training and recruitment will be vital for Toyota to address these anticipated shortages.
Skills and Qualifications

Toyota, a global automotive giant, demands a specific skillset from its employees, reflecting the intricacies of modern vehicle manufacturing and design. From meticulous technical expertise to strong interpersonal abilities, these skills are crucial for success within the company. The required qualifications vary depending on the specific role, encompassing education, experience, and specialized certifications. This section delves into the essential technical and soft skills sought after by Toyota, outlining the expected education and experience levels for different positions, and providing examples of advantageous qualifications for prospective candidates.
Technical Skills
The technical landscape of the automotive industry is constantly evolving. Toyota prioritizes employees with a strong foundation in automotive engineering, manufacturing processes, and relevant technologies. Proficiency in areas like mechanical engineering, electrical systems, and software development is highly valued.
- Automotive Engineering: Knowledge of vehicle design principles, engine mechanics, and powertrain systems. Examples include understanding internal combustion engines (ICE), hybrid systems, and electric vehicle (EV) technologies. Toyota’s emphasis on innovative technologies like hybrid and electric vehicles necessitates a deep understanding of these systems.
- Manufacturing Processes: Familiarity with Lean manufacturing principles, quality control procedures, and production techniques. Understanding of automated assembly lines and robotics is crucial for roles involving manufacturing and production.
- Software Development: Proficiency in software applications, programming languages, and software testing. This is increasingly important as vehicles become more sophisticated and rely on software for functions like diagnostics, entertainment systems, and driver-assistance features. Toyota’s focus on developing advanced driver-assistance systems (ADAS) requires skilled software engineers.
- Data Analysis: The ability to collect, analyze, and interpret data related to vehicle performance, production efficiency, and customer feedback. This is essential for optimizing processes, improving quality, and responding to customer needs. Data analysis skills are becoming increasingly important for decision-making in the modern automotive industry.
Soft Skills
Toyota values strong communication and collaboration skills in addition to technical expertise. Effective teamwork, problem-solving abilities, and a commitment to quality are highly sought-after attributes.
- Communication Skills: The ability to clearly convey technical information, receive feedback, and work effectively with diverse teams. Strong written and verbal communication skills are critical for conveying technical details to colleagues and stakeholders.
- Teamwork: The ability to collaborate effectively with colleagues from different backgrounds and disciplines. Toyota’s manufacturing processes often involve intricate teamwork across various departments.
- Problem-solving: The ability to identify and resolve complex issues in a timely and efficient manner. This is crucial in a dynamic environment where challenges and unexpected issues may arise in the design, manufacturing, or maintenance of vehicles.
- Adaptability: The ability to adapt to new technologies, processes, and changing market conditions. The automotive industry is constantly evolving, demanding a flexible approach to stay current and competitive.
Education and Experience Levels
The required education and experience levels for Toyota positions vary depending on the specific role. Entry-level positions often require a bachelor’s degree in engineering or a related field, while senior roles may necessitate advanced degrees and several years of relevant experience.
- Entry-Level Roles: Typically require a bachelor’s degree in mechanical engineering, electrical engineering, or a related field. Some positions may accept candidates with strong academic records and relevant internships.
- Mid-Level Roles: Often demand a bachelor’s degree and 2-5 years of experience in a relevant field. Advanced certifications and specialized training in specific automotive technologies may be beneficial.
- Senior-Level Roles: Usually require a master’s degree or a doctorate in engineering, along with 5+ years of experience in a specialized field. Extensive experience within Toyota or a similar automotive company is frequently considered an advantage.
Examples of Advantageous Qualifications
Beyond the core skills, several qualifications can significantly enhance an application.
- Certifications: Industry-recognized certifications in specific areas like automotive engineering, Lean manufacturing, or quality management systems can be beneficial for demonstrating specialized knowledge and competence.
- Projects and Portfolio: Demonstrating practical experience through personal projects or a portfolio showcasing design work or technical achievements can make a candidate stand out.
- Internships: Relevant internships or volunteer work in the automotive industry can provide valuable experience and insight into the workplace environment.
- Relevant Coursework: Specific coursework in areas like robotics, mechatronics, or data analytics can give applicants an edge in certain roles.
Toyota Car Manufacturing Processes
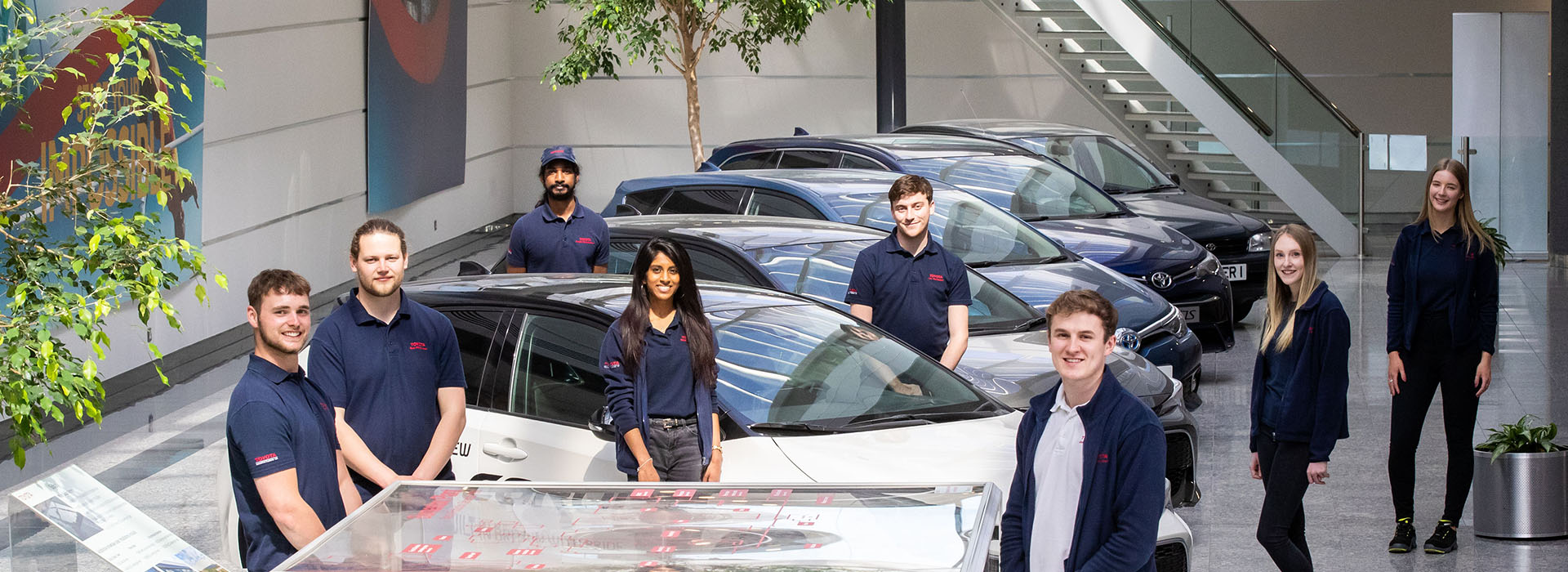
Toyota’s car manufacturing process is renowned for its efficiency and quality. This meticulous process, underpinned by the Toyota Production System (TPS), ensures vehicles are built to exacting standards. Understanding the stages and the roles of employees within each is crucial for anyone considering a career in the automotive industry.
Key Stages in the Toyota Manufacturing Process
The Toyota manufacturing process is a meticulously planned sequence of stages, each contributing to the final product. These stages are not isolated but rather interconnected and interdependent, ensuring smooth production flow and minimizing waste.
- Component Procurement and Inspection: This initial stage involves sourcing and inspecting parts from various suppliers. Rigorous quality checks are performed to ensure each component meets Toyota’s stringent standards. Purchasing agents and quality control inspectors play vital roles in this stage. Their responsibilities include verifying part specifications, confirming delivery schedules, and ensuring compliance with quality standards. Issues are identified and rectified before the components move to the next stage.
- Sub-Assembly and Module Building: Components are assembled into sub-assemblies and modules. Specialized teams of assembly line workers, technicians, and quality inspectors are responsible for accurately assembling these components. The meticulous nature of these teams is critical in maintaining the quality of the vehicle. Quality checks are performed at each step to detect defects and ensure precision in assembly.
- Vehicle Body Assembly: The body panels are assembled, welded, and fitted together. Welding operators, body panel installers, and robotic arms are employed in this stage. The efficiency and precision of these processes ensure the structural integrity of the vehicle body. Quality checks and inspections are performed at every stage of the body assembly.
- Paint Application and Finishing: The vehicle body is painted and finished to meet aesthetic standards. Painters, spray technicians, and finishing specialists apply coats of paint and ensure the final finish meets the required standards. The use of robotic painting systems, and careful control of paint application, is critical to quality and efficiency.
- Interior Assembly and Finishing: The interior components, including seats, dashboard, and other interior elements, are installed. Interior fitters and assemblers work together to ensure the correct placement and functionality of interior parts. A rigorous inspection process ensures the interior is aligned with the design specifications.
- Final Assembly and Testing: The complete vehicle is assembled, and a comprehensive series of tests are performed. Assembly line workers, technicians, and quality control inspectors perform the final assembly and testing, ensuring the functionality of all systems. Tests include engine performance, braking, suspension, and electrical systems. The final inspection process ensures the car meets all quality and safety standards.
Visual Representation of the Manufacturing Process
Imagine a flowchart, starting with the “Component Procurement” box. Arrows connect this box to “Sub-Assembly” and “Module Building”. From there, arrows lead to “Vehicle Body Assembly”. This stage then connects to “Paint Application and Finishing”, which in turn connects to “Interior Assembly and Finishing”. Finally, an arrow leads from “Interior Assembly and Finishing” to “Final Assembly and Testing”. Each box represents a stage, with specific job functions assigned to each section of the process. This visual demonstrates the sequential nature of the process and the crucial role of each team.
Employee Benefits and Compensation

Toyota prioritizes its employees’ well-being and financial security, offering a comprehensive benefits package designed to attract and retain top talent. The compensation structure reflects the diverse roles and responsibilities within the company, aligning compensation with performance and market trends. This section details the benefits, compensation structures, and compares Toyota’s offerings with those of competitors in the automotive industry.
Benefits Packages Offered by Toyota
Toyota’s benefits packages are designed to support employees’ overall well-being, encompassing a wide range of offerings. These packages often include health insurance options, retirement plans, paid time off, and professional development opportunities. The specific benefits offered may vary based on the employee’s role and location.
- Health insurance: Toyota typically offers a range of health insurance plans, including medical, dental, and vision coverage. These plans are often competitive and include options for various family sizes and individual needs.
- Retirement plans: Toyota’s retirement plans often include 401(k) or similar options, with potential company matching contributions. This allows employees to save for retirement and encourages long-term commitment.
- Paid time off: Employees are typically granted paid time off for vacation, sick leave, and holidays. The amount of paid time off can vary based on employment status and tenure.
- Professional development: Toyota often provides opportunities for professional development, such as training programs, workshops, and tuition reimbursement. This demonstrates a commitment to employee growth and skill enhancement.
Compensation Structures and Salary Ranges
Toyota’s compensation structures are generally market-competitive and consider various factors, including job level, experience, skills, and performance. Salaries for different roles within the company vary significantly, depending on the specific position and the individual’s qualifications. Entry-level positions typically have lower salary ranges compared to senior-level roles requiring extensive experience and specialized skills.
- Entry-level roles: Entry-level positions, such as production associates, typically fall within a specific salary range, depending on experience and education. These salaries are usually comparable to those of other manufacturing companies in the region.
- Mid-level roles: Mid-level roles, such as supervisors and team leaders, typically command higher salaries, often based on years of experience and demonstrable leadership skills.
- Senior-level roles: Senior-level roles, such as managers and executives, have the highest salary ranges, reflecting the complexity of their responsibilities and the high level of experience required.
Comparison with Competitors
Toyota’s compensation and benefits packages are benchmarked against those of its competitors in the automotive industry. Competitors like Honda, Nissan, and Ford often offer similar benefits, but specific details, such as health insurance premiums, retirement plan contributions, and paid time off policies, can differ.
Benefit/Compensation Aspect | Toyota | Honda | Nissan | Ford |
---|---|---|---|---|
Health Insurance Premiums | Competitive with market average | Slightly above market average | Slightly below market average | Variable depending on plan selected |
Retirement Plan Matching | Generally good match | Very good match | Average match | Variable match based on specific plan |
Paid Time Off | Standard industry average | Slightly above industry average | Slightly below industry average | Competitive but varies by position |
Training and Development Opportunities | Comprehensive programs | Strong focus on employee growth | Good, but less structured programs | Emphasis on specific skills training |
Career Development at Toyota
Toyota prioritizes employee growth and development, recognizing that a skilled and motivated workforce is crucial for its continued success. This commitment to career advancement fosters a culture of continuous learning and improvement, enabling employees to reach their full potential while contributing to Toyota’s strategic objectives. A strong focus on internal mobility allows employees to explore different roles and departments, adapting to changing needs and leveraging their expertise across various aspects of the organization.
Career progression within Toyota is facilitated through structured training programs and opportunities for specialized skill development. This comprehensive approach ensures employees possess the necessary competencies for advancing to more demanding roles, thereby supporting Toyota’s global operations and market competitiveness.
Career Advancement Pathways
Toyota offers a diverse range of career paths across its various departments, from manufacturing and engineering to sales and marketing. This multifaceted approach caters to employees with varied interests and skill sets, fostering a sense of purpose and accomplishment. Each pathway is designed to progressively develop expertise and leadership abilities, enabling employees to advance their careers within the company.
Training Programs and Development Initiatives
Toyota invests significantly in employee training, providing comprehensive programs designed to enhance technical skills and leadership abilities. These initiatives include:
- Technical Training Programs: These programs equip employees with specialized knowledge and skills in areas like automotive engineering, manufacturing processes, and quality control. They often involve hands-on training, simulations, and mentoring from experienced professionals.
- Leadership Development Programs: Designed to cultivate leadership qualities, these programs provide employees with opportunities to enhance their communication, decision-making, and problem-solving skills. They typically include workshops, seminars, and practical leadership assignments.
- Cross-Functional Training: To foster a broader understanding of Toyota’s operations, cross-functional training programs expose employees to different departments and functions. This provides valuable insights into the interconnectedness of various aspects of the company.
Internal Mobility Programs
Toyota recognizes the value of internal mobility, enabling employees to transition between different roles and departments within the company. This internal talent exchange allows for the development of versatile employees and ensures that the organization benefits from a wider range of expertise.
- Lateral Transfers: Employees can transfer to roles within different departments or functions based on their skills and interests. This allows for employees to explore new areas of expertise and expand their knowledge base.
- Promotions: Based on performance reviews, demonstrated skills, and qualifications, employees are eligible for internal promotions to higher-level positions.
- Mentorship Programs: Mentorship programs provide guidance and support to employees as they navigate their career paths, ensuring they gain valuable insights from experienced professionals.
Career Progression Pathways
Visual representation (without image links) of career progression pathways within Toyota. This conceptual illustration depicts a branching structure representing various departments and career paths. Starting from entry-level positions, the illustration shows multiple branches leading to specialized roles, supervisory positions, and managerial roles within various departments like engineering, manufacturing, sales, and administration.
Entry Level | Specialized Roles | Supervisory Roles | Management Roles |
---|---|---|---|
Technician | Engineer Specialist | Team Leader | Department Head |
Sales Associate | Sales Manager | Regional Manager | National Sales Director |
Manufacturing Operator | Quality Control Specialist | Production Supervisor | Plant Manager |
Each branch represents a potential career path, and employees can choose the path that aligns with their interests and aspirations. The pathways highlight the variety of opportunities for growth and advancement available within Toyota.