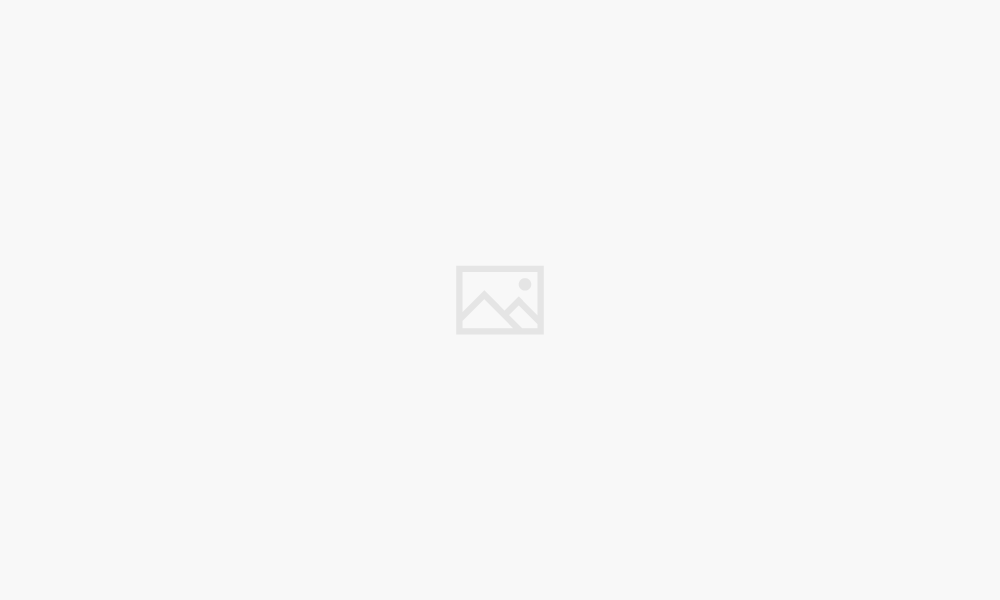
- Overview of Toyota Car Building
- Toyota Manufacturing Processes
- Toyota’s Supply Chain
-
Toyota’s Design and Engineering
- The Toyota Car Design Process
- Engineering Principles Behind Toyota’s Vehicles
- Key Design Considerations in Toyota’s Vehicles
- Comparison of Toyota’s Car Design Philosophy with Other Manufacturers
- Toyota’s Approach to Safety Features and Technology Integration
- Use of Computer-Aided Design (CAD) and Simulation in Toyota’s Design Process
- Toyota’s Impact on the Automotive Industry
- Future of Toyota Car Building
Overview of Toyota Car Building
Toyota’s journey in automotive manufacturing is a testament to innovation and relentless pursuit of quality. From humble beginnings, the company has risen to become a global leader, shaping the industry through technological advancements and a commitment to customer satisfaction. This overview delves into Toyota’s history, key milestones, design philosophy, product range, and competitive strategies in the automotive arena.
Toyota’s Historical Development
Toyota Motor Corporation’s origins lie in the post-World War II era. Initially focused on producing small, affordable vehicles, the company quickly established a reputation for reliability and efficiency. The company’s commitment to continuous improvement and its early adoption of lean manufacturing principles laid the groundwork for its future success. This initial focus on practicality and affordability, combined with a meticulous approach to production, would become cornerstones of Toyota’s strategy.
Key Milestones in Manufacturing Processes
Toyota’s advancements in manufacturing processes have been pivotal to its success. The development of the Toyota Production System (TPS), characterized by just-in-time inventory management and continuous improvement, revolutionized the automotive industry. This system, incorporating automation, standardized work procedures, and a culture of problem-solving, minimized waste and maximized efficiency. The introduction of automation and robotics further refined production lines, leading to higher output and improved quality control.
Toyota’s Design and Engineering Philosophy
Toyota’s approach to vehicle design emphasizes practicality, fuel efficiency, and safety. The company strives for a balance between performance and economy, reflecting a customer-centric design philosophy. A core principle is the meticulous integration of design and engineering, ensuring that aesthetic appeal aligns with functional performance. This integration prioritizes durability, reliability, and a user-friendly driving experience.
Vehicle Portfolio
Toyota’s product range encompasses a wide spectrum of vehicles, catering to diverse needs and preferences. From compact cars to SUVs, from trucks to hybrid and electric vehicles, Toyota’s portfolio demonstrates its commitment to providing a comprehensive range of transportation solutions. The company’s adaptability in responding to evolving consumer demands ensures a continuous evolution in its offerings.
Comparison with Other Major Automakers
Compared to other major automakers, Toyota’s strategy emphasizes efficiency, reliability, and a focus on core competencies. While competitors might prioritize cutting-edge technology or distinctive designs, Toyota prioritizes a balanced approach, combining innovation with proven reliability. This strategic focus has enabled Toyota to build a strong brand reputation, fostering customer loyalty and a significant global presence.
Timeline of Key Events
Year | Event |
---|---|
1937 | Toyota Motor Corporation founded |
1950s | Development of the Toyota Production System (TPS) |
1970s | Introduction of fuel-efficient models, solidifying reputation for reliability |
1990s | Expansion into global markets, increased investment in research and development |
2000s | Emphasis on hybrid technology, introduction of first mass-market hybrid vehicles |
2010s | Focus on electrification, increased production of hybrid and electric vehicles |
Toyota Manufacturing Processes

Toyota’s meticulous manufacturing processes are a cornerstone of its global success. These processes, built on a foundation of lean principles and advanced technology, are instrumental in producing high-quality vehicles efficiently. From initial design to final assembly, each stage is carefully orchestrated to maintain a high level of precision and quality.
The Toyota Production System (TPS) is a sophisticated methodology that drives the entire manufacturing process. TPS emphasizes continuous improvement, eliminating waste, and empowering employees to identify and resolve issues. This iterative approach ensures that every step in the car-building process is optimized for efficiency and effectiveness.
Stages of Toyota Car Building
The journey of a Toyota car from concept to showroom involves a series of meticulously planned and executed stages. Each stage builds upon the previous one, with a focus on quality control and adherence to strict standards. The process begins with the design phase, then moves through various manufacturing steps before reaching the final assembly line.
- Design and Engineering: Initial conceptualization and design of the vehicle are crucial. Engineers utilize computer-aided design (CAD) software and simulations to develop the car’s structure, features, and performance specifications. Thorough testing and validation ensure that the design meets safety and performance standards. Prototypes are created and extensively tested before production begins. This stage includes detailed engineering drawings, material selection, and part specifications.
- Component Production: Specialized factories produce individual vehicle components like engines, transmissions, and body panels. These factories often employ highly automated processes for precision and speed. Strict quality control measures are implemented throughout this stage to ensure each component meets the required specifications. Advanced machinery and robotics are used to manufacture components efficiently and consistently.
- Sub-assembly: Individual components are assembled into sub-assemblies, such as engine units or chassis. This stage involves careful fitting and alignment of parts, often with the help of robots and automated systems. Quality checks are performed at each step to identify and correct any potential issues. Strict tolerances are maintained for consistent quality and performance.
- Final Assembly: The final assembly line brings all the sub-assemblies together to form a complete vehicle. This stage is highly automated, with robots performing many tasks to ensure precision and speed. Human workers perform critical tasks that require dexterity and judgment, like installing electrical systems and completing interior fittings. Quality control is rigorous at this stage, with checks performed at every station to ensure the car meets all specifications.
- Testing and Inspection: Once assembled, each vehicle undergoes rigorous testing to ensure its safety, performance, and reliability. Tests cover aspects like braking, acceleration, handling, and emissions. Inspection processes verify that the car meets all regulatory requirements. This stage often involves sophisticated testing equipment and trained personnel.
Lean Manufacturing Principles
Toyota’s production process is deeply rooted in lean manufacturing principles. These principles aim to eliminate waste (muda) in all aspects of production. This leads to increased efficiency, reduced costs, and improved quality.
- Just-in-Time (JIT) Inventory Management: JIT systems ensure that components are delivered to the assembly line precisely when needed. This minimizes inventory costs and storage space requirements. The focus is on delivering the right parts at the right time, avoiding delays and excess stock.
- Kaizen: Kaizen emphasizes continuous improvement. Employees at all levels are encouraged to identify and suggest improvements in processes and procedures. This culture of continuous learning and innovation leads to incremental improvements in efficiency and quality.
- 5S Methodology: 5S is a workplace organization system. It emphasizes organizing the workspace, standardizing procedures, and maintaining a clean and efficient environment. This helps to improve productivity and reduce errors.
Automation and Robotics
Toyota heavily utilizes automation and robotics in its manufacturing facilities. This reduces human error, increases production speed, and improves overall efficiency.
- Robotic Welding and Painting: Robots are extensively used for tasks like welding and painting, ensuring consistent quality and speed. These robots are programmed for precise movements and can perform tasks that would be difficult or impossible for humans.
- Automated Material Handling: Automated guided vehicles (AGVs) and other systems transport materials efficiently throughout the factory, minimizing the need for manual handling and reducing transport time.
- Automated Inspection Systems: Automated inspection systems are used to check parts and finished vehicles for defects. These systems can detect flaws that are difficult for human inspectors to spot.
Worker Roles and Responsibilities
Toyota’s manufacturing process relies on a diverse workforce with various roles and responsibilities. Employees are trained in multiple aspects of the production process, empowering them to be versatile and adaptable.
- Production Workers: These workers perform tasks like assembly, inspection, and machine operation. They are crucial for the smooth functioning of the assembly line.
- Engineers and Technicians: Engineers and technicians maintain and troubleshoot machinery, ensuring that production processes run smoothly. They are vital in identifying and resolving technical issues.
- Quality Control Personnel: These workers are responsible for ensuring that the quality standards are met at every stage of the process. They conduct inspections and identify defects.
Quality Control Measures
Maintaining the high quality of Toyota vehicles is a top priority. Various quality control measures are implemented throughout the manufacturing process.
- Statistical Process Control (SPC): SPC techniques are used to monitor and control production processes, identifying and correcting deviations from standards.
- Inspection at Each Stage: Inspections are performed at every stage of the process to identify and rectify defects. This ensures that defects are caught early in the process, minimizing their impact.
- Regular Audits: Regular audits are conducted to verify that quality control procedures are being followed effectively. These audits help to maintain consistency and identify areas for improvement.
Toyota Car Production Stages
Stage | Description | Time Estimate (Days) |
---|---|---|
Design and Engineering | Conceptualization, design, testing | 60-90 |
Component Production | Manufacturing of individual components | 30-60 |
Sub-assembly | Assembling components into sub-assemblies | 15-25 |
Final Assembly | Bringing sub-assemblies together to form a vehicle | 5-10 |
Testing and Inspection | Rigorous testing and inspection of assembled vehicles | 3-5 |
Toyota’s Supply Chain
Toyota’s success in the automotive industry is intrinsically linked to its sophisticated and highly efficient supply chain. This intricate network of suppliers, manufacturers, and distributors is crucial for delivering high-quality vehicles at competitive prices. Understanding the intricacies of Toyota’s supply chain provides valuable insights into the company’s operational excellence.
Importance of Toyota’s Supply Chain
Toyota’s supply chain is not merely a logistics system; it’s a strategic asset. It ensures the timely and cost-effective procurement of raw materials, components, and parts, crucial for maintaining production schedules and minimizing operational costs. A robust supply chain also fosters a stable and reliable relationship with suppliers, leading to improved product quality and reduced risk. The efficiency and responsiveness of this system are key factors in Toyota’s ability to react quickly to market demands and maintain a competitive edge.
Strategies for Effective Supply Chain Management
Toyota employs a variety of strategies to maintain an effective and responsive supply chain. A core principle is Just-in-Time (JIT) inventory management, minimizing storage costs and ensuring materials are delivered precisely when needed. Furthermore, Toyota prioritizes long-term relationships with key suppliers, fostering collaboration and mutual trust. This approach enables efficient communication and problem-solving, facilitating the seamless flow of information and resources. Another vital strategy is the use of Kanban systems, which visually track inventory levels and signal the need for replenishment.
Key Suppliers and Their Contributions
Toyota maintains a network of carefully selected suppliers, each contributing specific expertise and resources. Major suppliers in the automotive industry often provide critical components such as engines, transmissions, electronics, and body panels. Their expertise and technological advancements are integral to Toyota’s ability to deliver innovative and high-quality vehicles. These suppliers often have long-standing partnerships with Toyota, contributing to the smooth and efficient operation of the supply chain.
Comparison to Other Car Manufacturers
Toyota’s supply chain management is often cited as a benchmark for other automotive manufacturers. While other companies also utilize JIT and other strategies, Toyota’s comprehensive approach, emphasizing long-term relationships and continuous improvement, distinguishes its system. This focus on collaboration and efficiency often results in a more responsive and cost-effective supply chain. A key difference lies in the level of integration Toyota cultivates with its suppliers.
Challenges and Opportunities in Toyota’s Supply Chain
Like any complex system, Toyota’s supply chain faces challenges. Geopolitical instability, natural disasters, and global pandemics can disrupt the flow of materials and impact production schedules. The increasing demand for electric vehicles and advanced technologies also presents both challenges and opportunities. Adapting to these evolving demands and maintaining a resilient supply chain is essential for continued success.
Visual Representation of Material Flow
Stage | Description |
---|---|
Raw Material Sourcing | Procurement of raw materials (e.g., steel, plastics) from various suppliers. |
Component Manufacturing | Suppliers manufacture components (e.g., engines, transmissions) according to Toyota’s specifications. |
Assembly Line | Toyota assembles components into vehicles at their manufacturing plants. |
Logistics & Distribution | Vehicles are transported to dealerships and consumers via a complex network of logistics providers. |
Customer Feedback | Customer feedback and market trends inform Toyota’s future supply chain strategy. |
Toyota’s Design and Engineering
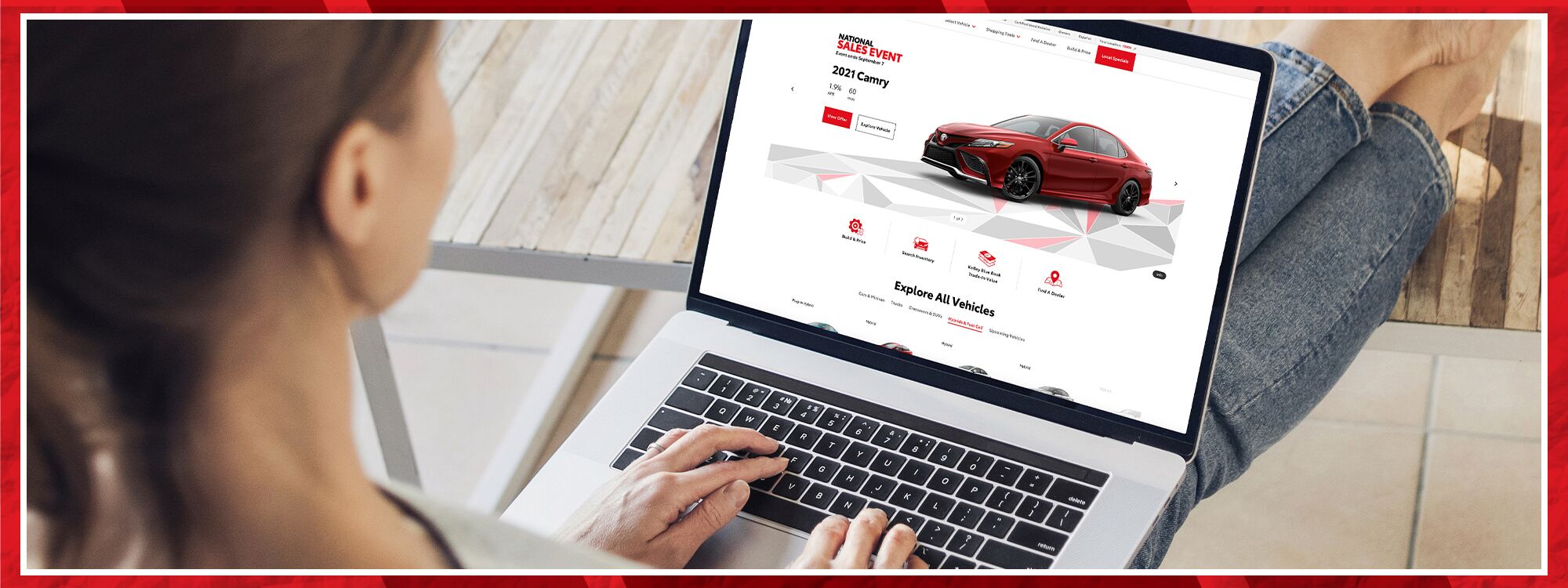
Toyota’s design and engineering prowess are crucial to its global success. The company meticulously crafts vehicles that balance performance, safety, and efficiency. This involves a complex process, from initial concept to final production, incorporating rigorous testing and meticulous attention to detail. Toyota’s commitment to these aspects reflects in its extensive product portfolio, including a wide range of models catering to diverse customer needs.
The Toyota Car Design Process
Toyota’s car design process is a multi-stage approach, beginning with conceptualization and progressing through various stages of refinement and testing before production. The process prioritizes customer feedback and market analysis to ensure the final product aligns with consumer expectations. Each stage is critical to the success of the final vehicle.
Engineering Principles Behind Toyota’s Vehicles
Toyota vehicles are renowned for their reliability and efficiency. These qualities are rooted in Toyota’s engineering principles, which prioritize quality control and lean manufacturing techniques. The company strives for minimal waste and maximum efficiency in every aspect of production, resulting in robust and reliable vehicles. A key component of this is the focus on continuous improvement and problem-solving.
Key Design Considerations in Toyota’s Vehicles
Several key design considerations drive Toyota’s vehicle development. These include fuel efficiency, safety features, interior comfort, and exterior aesthetics. Toyota engineers meticulously balance these factors to create vehicles that are not only attractive but also functional and safe. This involves extensive market research and customer feedback to ensure the vehicles resonate with target audiences. A primary example is Toyota’s commitment to hybrid technology, reflecting a dedication to environmentally friendly vehicles.
Comparison of Toyota’s Car Design Philosophy with Other Manufacturers
Toyota’s design philosophy contrasts with some competitors, emphasizing reliability and practicality over flashy design elements. While some manufacturers prioritize bold aesthetics, Toyota focuses on a more understated and functional approach. This difference is apparent in the vehicles’ overall design language and feature sets. The Toyota approach often prioritizes efficiency and durability over immediate visual appeal.
Toyota’s Approach to Safety Features and Technology Integration
Safety is paramount in Toyota’s design philosophy. The company incorporates advanced safety features, including airbags, anti-lock brakes, and electronic stability control, as standard equipment. Moreover, Toyota is a leader in integrating advanced driver-assistance systems (ADAS) into its vehicles, aiming to improve both driver and passenger safety. This reflects a commitment to proactively addressing safety concerns and incorporating cutting-edge technology.
Use of Computer-Aided Design (CAD) and Simulation in Toyota’s Design Process
Toyota extensively utilizes computer-aided design (CAD) and simulation tools to optimize the design process. These tools allow engineers to virtually test and refine designs before physical prototypes are created, saving time and resources. This digital approach allows for more precise adjustments and the ability to simulate various scenarios to identify potential issues early in the development cycle. By leveraging these tools, Toyota ensures greater accuracy and efficiency.
Toyota’s Impact on the Automotive Industry
Toyota’s influence on the global automotive industry is profound and multifaceted. From its pioneering lean manufacturing system to its innovative hybrid technologies, Toyota has consistently pushed the boundaries of automotive design, production, and sustainability. Its impact extends beyond the factory floor, shaping consumer expectations and influencing the industry’s future trajectory.
Toyota’s relentless pursuit of efficiency and quality has redefined automotive manufacturing. This dedication to continuous improvement, coupled with its astute understanding of market demands, has positioned Toyota as a dominant force in the global automotive landscape. This influence is clearly visible in the industry’s ongoing adoption of similar production methodologies and the continued interest in hybrid and electric vehicle technologies.
Toyota’s Influence on Manufacturing Processes
Toyota’s lean manufacturing system, a cornerstone of its success, has had a significant impact on the automotive industry. The system, emphasizing waste reduction, continuous improvement, and worker empowerment, has been adopted and adapted by numerous manufacturers globally. This methodology prioritizes efficiency and quality control, leading to reduced costs and improved product quality. The principles of Just-in-Time inventory management and the 5S methodology, integral parts of Toyota’s system, are now commonplace in manufacturing sectors beyond automobiles.
Innovations in Automotive Technology
Toyota has been a leader in introducing several groundbreaking innovations in the automotive industry. The development and popularization of hybrid vehicles, exemplified by the Prius, dramatically changed the landscape of fuel efficiency and reduced emissions. Toyota’s investment in research and development of electric vehicle technology is also reshaping the future of mobility. Other notable innovations include advanced safety features and driver-assistance systems, significantly improving road safety and driving experience.
Toyota’s Contribution to Sustainable Practices
Toyota’s commitment to sustainability extends beyond its hybrid and electric vehicles. The company has actively sought to reduce its environmental footprint throughout its manufacturing processes. This includes reducing waste, improving energy efficiency, and utilizing sustainable materials in its vehicles. Toyota’s focus on sustainable practices has set an example for other automakers, inspiring them to adopt similar initiatives and encouraging a more environmentally conscious approach to car manufacturing. Furthermore, Toyota’s dedication to recycling and reuse within its supply chain demonstrates a comprehensive commitment to sustainable operations.
Global Presence and Market Share
Toyota’s global presence is substantial, with a significant market share in numerous countries. The company’s extensive network of manufacturing facilities and distribution channels allows for efficient production and delivery of vehicles across the globe. This broad global reach provides Toyota with significant competitive advantages, allowing it to adapt to diverse regional preferences and demands. Toyota’s ability to adapt to local market needs and tailor its offerings to specific preferences distinguishes it from competitors. Comparing Toyota’s global presence with that of other major automakers reveals a clear commitment to global expansion and a well-established presence in numerous regions.
Shaping the Future of Automotive Technology
Toyota’s role in shaping the future of automotive technology is undeniable. The company’s continued investment in research and development of electric vehicles, autonomous driving systems, and connected car technologies positions it at the forefront of innovation. These developments are likely to significantly impact how people interact with and experience automobiles in the years to come. For example, Toyota’s recent advancements in autonomous driving technology have been widely recognized and praised for their safety features and technological sophistication.
Quote from an Automotive Industry Leader
“Toyota’s impact on the automotive industry is unparalleled. Their commitment to innovation, quality, and sustainability has set a new standard for the entire sector. Their lean manufacturing principles and groundbreaking technologies are truly transformative.” – [Name of a prominent automotive industry leader]
Future of Toyota Car Building

Toyota, a cornerstone of the automotive industry, faces a dynamic future demanding adaptability and innovation. The company’s success hinges on its ability to navigate evolving consumer preferences, embrace emerging technologies, and strategically position itself in the rapidly changing landscape of the automotive market. This involves a comprehensive approach, encompassing advancements in electric vehicles, alternative fuels, manufacturing processes, and consumer engagement.
Toyota’s long-standing commitment to quality and reliability will be crucial in its future endeavors. Maintaining these core values while incorporating cutting-edge technologies will be key to achieving sustained success. Moreover, the company must anticipate and respond to changing consumer demands and market trends to remain competitive.
Electric Vehicle Strategy and Adoption
Toyota’s transition to electric vehicles (EVs) is a significant step towards sustainability and a changing market. The company has a substantial portfolio of hybrid vehicles, demonstrating its ability to develop and integrate alternative powertrains. The future will see a greater emphasis on fully electric models, coupled with the development of innovative charging infrastructure and battery technology. This approach reflects Toyota’s long-term vision for a sustainable automotive future.
Alternative Fuels and Powertrains
The exploration of alternative fuels and powertrains is crucial for Toyota’s long-term strategy. Hydrogen fuel cell vehicles represent a significant area of focus, offering potential for zero-emission driving. Further exploration into sustainable biofuels and other advanced technologies will be necessary to address the evolving energy landscape and consumer preferences. Toyota’s commitment to developing comprehensive solutions across various fuel types positions it well for the future.
Adoption of New Technologies in Manufacturing
Toyota’s manufacturing processes are known for their efficiency and precision. The future will see the integration of advanced technologies like automation, robotics, and artificial intelligence to further optimize production lines. This includes the use of 3D printing for customized parts and the implementation of data analytics to predict and prevent potential issues. These advancements will improve production efficiency, reduce costs, and enhance product customization.
Challenges and Opportunities
The automotive industry faces several challenges, including fluctuating raw material costs, the complexity of integrating new technologies, and maintaining profitability in a rapidly changing market. Opportunities include the potential for market expansion into emerging markets and the ability to capture new consumer segments through innovative product design. Toyota must adapt to these challenges and capitalize on the available opportunities to maintain its position as a global leader.
Adapting to Evolving Consumer Preferences
Consumer preferences are constantly evolving, with a growing demand for personalization, connectivity, and sustainability. Toyota will need to adapt its design and marketing strategies to cater to these demands. This involves providing customers with a range of customization options, integrating advanced infotainment systems, and highlighting the environmental benefits of its vehicles.
Potential Future Technologies and Implications
Potential Future Technology | Implications for Toyota’s Car-Building Processes |
---|---|
Autonomous Driving Systems | Significant changes in manufacturing, requiring advanced sensors, software, and safety systems. Potential for increased efficiency and reduced labor costs. |
Advanced Materials | Opportunities to create lighter, stronger, and more sustainable vehicles. Requires partnerships with material suppliers and process adjustments. |
Connected Car Technology | Integration of communication and data management systems, demanding significant investment in software and infrastructure. Enhances customer experience and vehicle performance. |
Artificial Intelligence (AI) in Design and Engineering | Streamlining the design and engineering process, leading to faster product development cycles. Requires significant investment in AI capabilities and talent. |