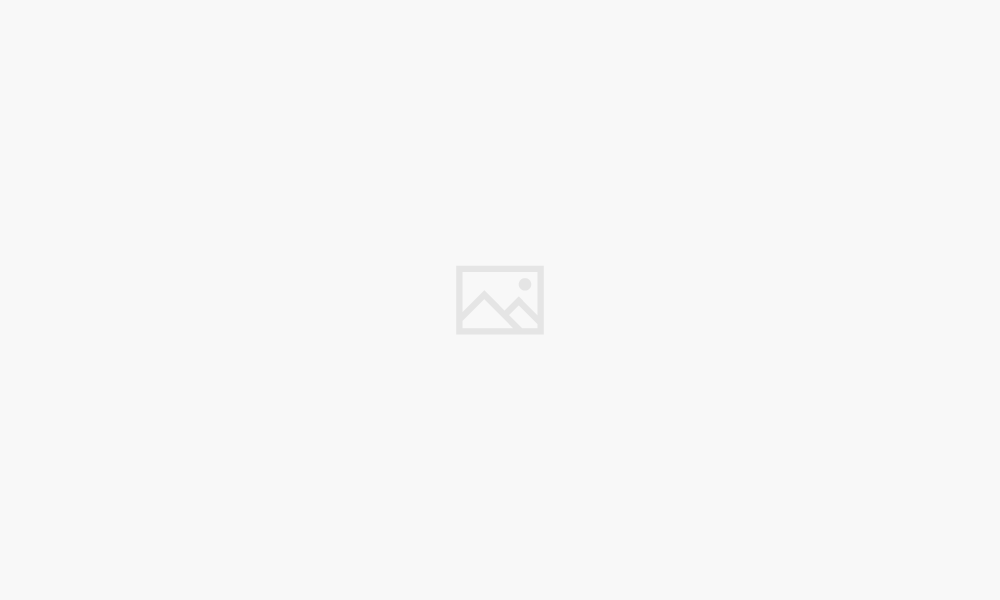
BMW USA Manufacturing Overview
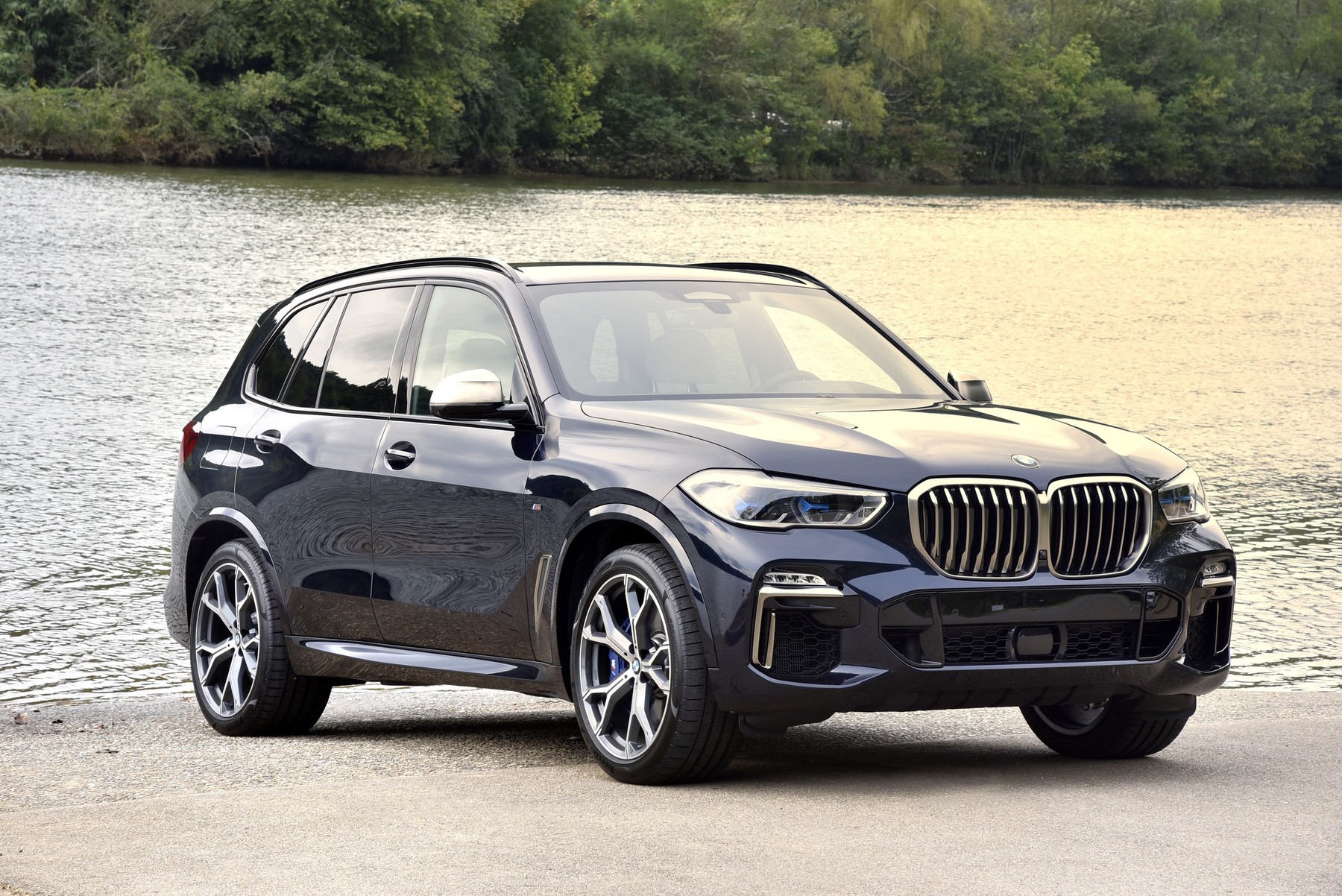
BMW’s manufacturing presence in the USA reflects its commitment to the North American market and its global strategy. The company’s US facilities are strategically located to support regional demand and optimize supply chains. These facilities are integral to BMW’s production and distribution network, showcasing a significant investment in the American economy.
BMW’s US manufacturing operations have evolved considerably over time, adapting to changing market demands and technological advancements. This evolution is evident in the diverse range of vehicles produced at each location and the ongoing improvements in production processes and facility capacities.
BMW Manufacturing Facility Locations in the USA
BMW operates several manufacturing facilities in the USA, each contributing to its overall production capacity and regional presence. These facilities play a critical role in meeting the demand for BMW vehicles in the North American market and supporting local economies.
Vehicle Production at Each Facility
The different BMW facilities in the USA specialize in various vehicle types. This specialization allows for efficient production and caters to diverse customer preferences. The types of vehicles produced at each location are carefully considered, ensuring that each facility aligns with the specific needs of its local market.
Production Capacity and Scale
The scale and capacity of each BMW US manufacturing facility vary significantly. These differences reflect the specific production needs and market demands at each location. The production capacity of each facility is crucial for meeting the growing demand for BMW vehicles and ensuring a smooth supply chain.
Summary Table of US Manufacturing Facilities
Facility Location | Vehicle Types | Production Capacity |
---|---|---|
Spartanburg, South Carolina | X5, X6, X7, X3, X4, and related vehicles (including plug-in hybrid versions) | Approximately 400,000 vehicles annually. This capacity has seen adjustments over time, often in response to market fluctuations and technological advancements. |
Woodridge, Illinois | 3-Series, 4-Series, and 5-Series vehicles (including plug-in hybrid versions). | Approximately 200,000 vehicles annually. The facility’s capacity has been adjusted in response to demand and product diversification. |
San Luis Potosí, Mexico (part of the North American network) | X1, X3, and certain other models | Approximately 300,000 vehicles annually. The facility, while located in Mexico, is integrated into the overall North American BMW production network. This is a key element in maintaining responsiveness to market fluctuations and regional demand. |
Supply Chain and Sourcing
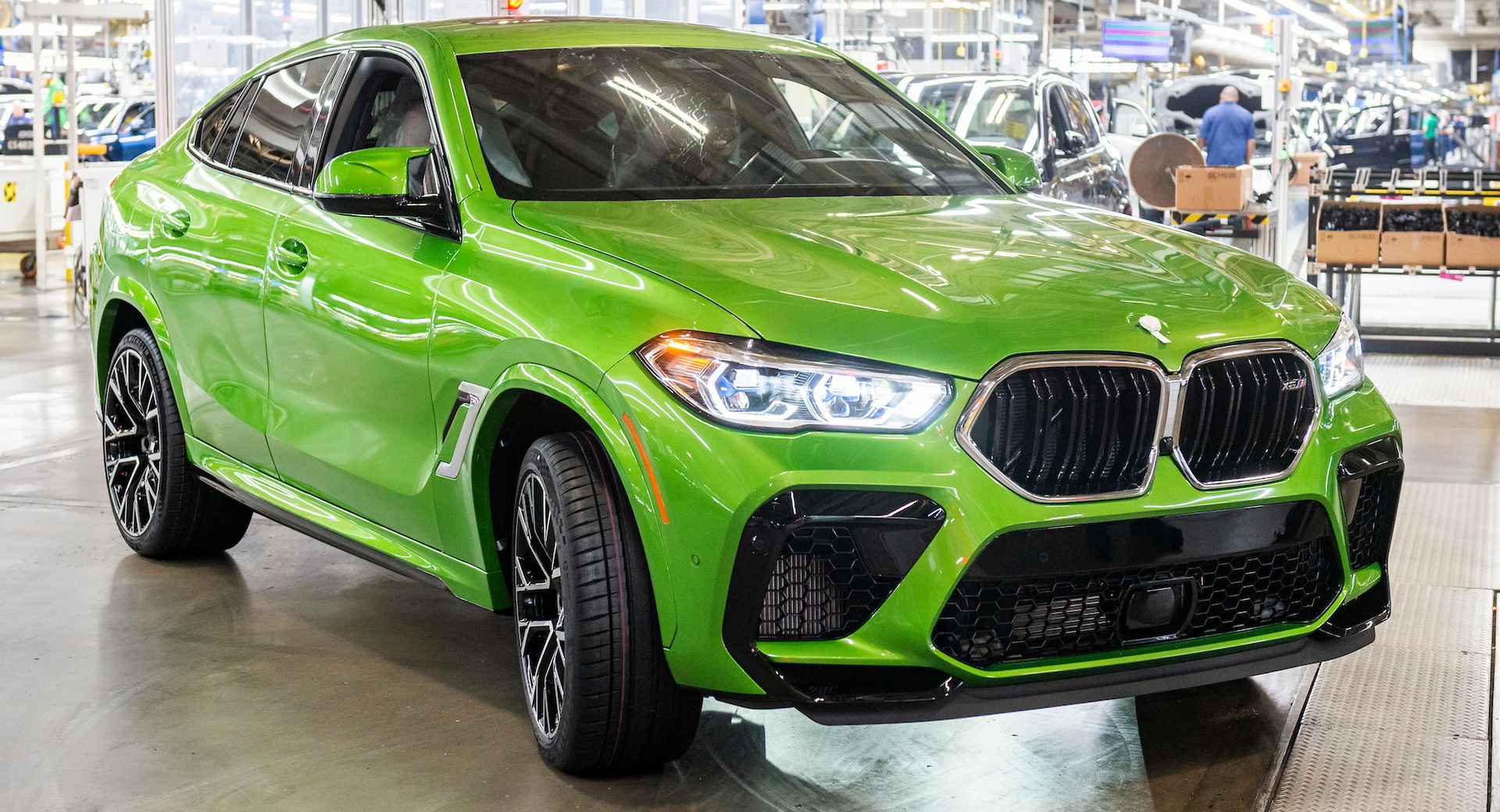
BMW’s US manufacturing operations rely heavily on a robust and intricate supply chain. This intricate network is critical for delivering high-quality vehicles efficiently and cost-effectively. The complexity arises from the diverse components required for each model, the varying levels of sophistication, and the global nature of the automotive industry. Understanding the sourcing strategies and the geographical distribution of suppliers is crucial for evaluating the overall efficiency and resilience of this network.
The supply chain for BMW USA vehicles involves a global network of suppliers, carefully selected for their expertise, quality, and reliability. This necessitates a nuanced approach to sourcing, balancing factors like cost, lead times, and potential geopolitical risks. Strategies vary significantly depending on the specific component, from sophisticated engineering parts to readily available raw materials. This diversity in sourcing strategies highlights the complexity and strategic importance of managing the supply chain.
Key Suppliers for BMW USA Production
BMW USA production relies on a diverse array of suppliers, each contributing specific components. These suppliers range from established global players to specialized regional companies. This diversity ensures a robust and adaptable supply chain. The selection of these suppliers is driven by factors including quality control, production capacity, and the supplier’s ability to adhere to BMW’s stringent standards.
Comparison of Sourcing Strategies for Different Vehicle Components
Sourcing strategies vary significantly across different vehicle components. For instance, critical engine components often involve long-term partnerships with strategically selected suppliers, ensuring consistent quality and potentially lower production costs. Meanwhile, materials like certain plastics or coatings might be sourced from a wider range of suppliers, depending on cost-effectiveness and availability. This strategic differentiation ensures the optimal balance between quality and cost-efficiency.
Geographical Distribution of Suppliers
Suppliers are geographically dispersed globally. Some suppliers are based in the United States, supporting domestic production and contributing to the US economy. However, many crucial components originate from other regions, particularly in Asia and Europe, reflecting the global nature of the automotive industry. This distribution creates both opportunities and challenges, necessitating careful management of logistics and potential geopolitical risks.
Importance of Domestic Sourcing for US Production
Domestic sourcing for US production is strategically important for several reasons. It strengthens the US automotive supply chain, supporting American jobs and fostering economic growth within the country. Furthermore, domestic suppliers often have a better understanding of local regulations and logistical requirements. The reliance on domestic suppliers also reduces lead times and improves the resilience of the supply chain in the face of global disruptions.
Major Suppliers and Their Contributions
The following table Artikels some major suppliers and their contributions to the BMW USA supply chain. This is not an exhaustive list but provides a glimpse into the breadth of the supplier network.
Supplier | Component | Country of Origin |
---|---|---|
Tier 1 Supplier A | Engine Components | Germany |
Tier 2 Supplier B | Interior Trim | Japan |
Tier 1 Supplier C | Exterior Body Panels | United States |
Tier 2 Supplier D | Electronics | South Korea |
Tier 1 Supplier E | Suspension Systems | United States |
Manufacturing Processes and Technologies
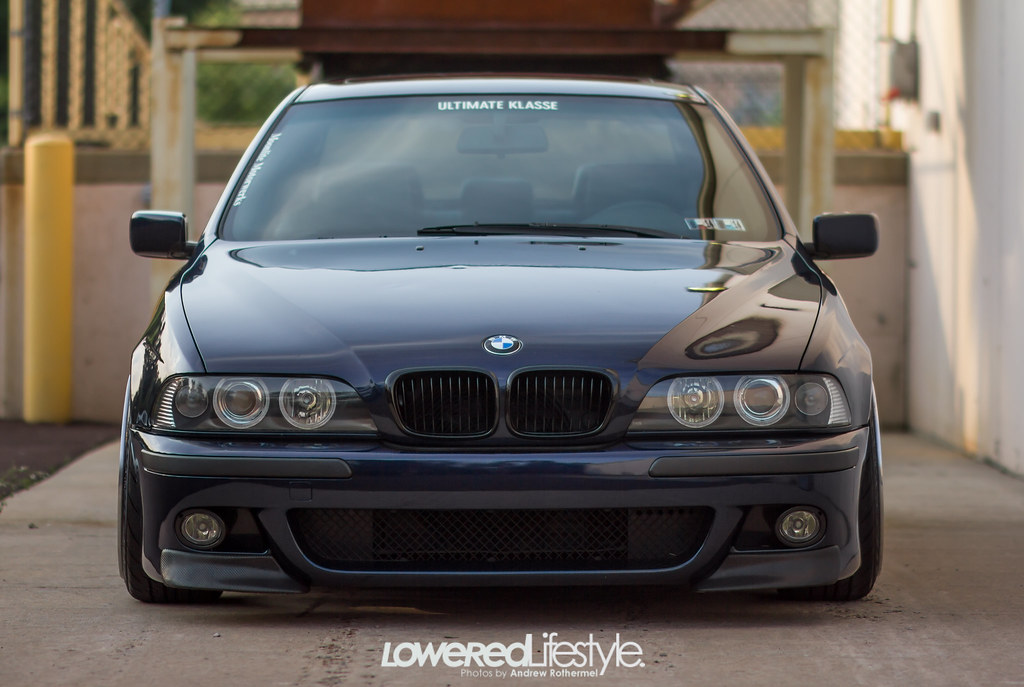
BMW’s US manufacturing facilities leverage a combination of traditional and cutting-edge techniques to produce high-quality vehicles. These processes are crucial to maintaining the brand’s reputation for precision engineering and customer satisfaction. The company’s commitment to innovation and efficiency ensures that vehicles meet stringent quality standards and are delivered on time.
Key Manufacturing Processes
BMW’s US plants employ a sophisticated array of manufacturing processes. These processes, meticulously planned and executed, are designed to maximize efficiency and minimize waste. From initial component assembly to final vehicle inspection, every stage is carefully optimized.
- Body Assembly: This stage involves the precise joining of various body panels and sub-assemblies. Robots and automated systems perform intricate welding and fastening tasks, ensuring high precision and consistency. Quality control measures, including visual inspections and dimensional checks, are implemented throughout the process.
- Paint Application: Sophisticated paint booths and automated spraying systems are employed to apply a uniform and durable paint finish. Precise control over temperature, humidity, and paint application parameters ensures a consistent, high-quality finish.
- Final Assembly: This crucial stage brings together all components to create the complete vehicle. Teams of highly skilled technicians, assisted by automated systems for tasks like engine installation and electrical connections, perform final checks and adjustments. Quality checks are rigorous, ensuring every vehicle meets BMW’s exacting standards.
- Component Manufacturing: BMW’s US plants receive many components from other facilities, both domestic and international. The integration of these parts into the final assembly line is a critical part of the manufacturing process, requiring precise coordination and logistics.
Advanced Technologies and Automation
Automation plays a significant role in BMW’s US manufacturing processes. The utilization of robots, advanced sensors, and data analytics systems streamlines operations and enhances efficiency.
- Robotics: Robots are extensively used for tasks ranging from welding and painting to handling and material movement. Their precision and speed enhance output and minimize human error.
- Automated Guided Vehicles (AGVs): AGVs transport components and materials throughout the manufacturing facilities, optimizing logistics and minimizing downtime.
- Computer-Aided Design (CAD) and Manufacturing (CAM): CAD/CAM software is used for designing and simulating manufacturing processes, allowing for optimization and preemptive problem-solving. This technology enables better coordination between different stages of production.
- Data Analytics: BMW leverages data analytics to track production metrics, identify bottlenecks, and predict potential issues. This approach allows for proactive measures to improve efficiency and quality.
Quality Control Measures
Maintaining high quality is paramount in BMW’s manufacturing process. A multi-layered approach ensures that each vehicle meets the company’s stringent standards.
- Inspection Stations: Numerous inspection stations are strategically located throughout the production line to identify defects early in the process. This proactive approach helps minimize costly repairs and rework later on.
- Testing Procedures: Thorough testing procedures are implemented to evaluate the performance and functionality of various components and systems. This comprehensive testing ensures that every vehicle meets performance and safety requirements.
- Statistical Process Control (SPC): SPC methods are used to monitor process variations and maintain consistency. This continuous monitoring allows for adjustments and improvements to be made in real-time.
Innovative Manufacturing Techniques
BMW is continuously seeking ways to improve its manufacturing processes. Innovative techniques, such as lean manufacturing principles, are implemented to optimize efficiency and minimize waste.
- Lean Manufacturing: The implementation of lean manufacturing principles, focusing on waste reduction and efficiency optimization, helps maintain production flow. This methodology helps improve the entire production process from initial design to final assembly.
- Just-in-Time Inventory Management: This system ensures that components are delivered only when needed, reducing storage costs and minimizing inventory waste.
Impact on the US Economy
BMW’s US manufacturing operations have a significant and multifaceted impact on the American economy. From job creation and investment in local communities to stimulating related industries, the company’s presence contributes substantially to the overall economic health of the nation. This impact extends beyond the immediate factory floor, influencing supply chains and fostering innovation across various sectors.
Economic Impact of Manufacturing Operations
BMW’s US plants contribute substantially to the local and national economy through direct employment and indirect job creation. The company’s investments in infrastructure and equipment, along with the production of high-quality vehicles, foster economic growth. These effects ripple through the economy, stimulating related industries such as parts manufacturing, logistics, and associated service sectors. This multifaceted impact makes BMW a crucial component of the American economic landscape.
Job Creation and Employment Statistics
BMW’s US manufacturing facilities are major employers. The company directly employs thousands of individuals in various roles, from production workers to engineers and managers. Beyond direct employment, BMW’s presence stimulates the growth of supporting industries, creating numerous indirect jobs. These include positions in parts manufacturing, transportation, and retail. The combined effect is a significant contribution to the overall employment figures in the regions where BMW operates. A comprehensive analysis of employment statistics, both direct and indirect, reveals the substantial economic impact of BMW’s US manufacturing.
Contribution to Local Communities
BMW’s US manufacturing facilities contribute significantly to the communities in which they are located. The company’s investments extend beyond employment to encompass community development initiatives. These may include funding local infrastructure projects, supporting educational programs, and contributing to social welfare programs. The long-term commitment to community engagement underscores the company’s responsibility beyond economic output. The benefits of BMW’s presence extend to improved infrastructure, enhanced educational opportunities, and an overall higher quality of life for local residents.
Impact on Related Industries
BMW’s US manufacturing operations have a profound impact on related industries, including parts manufacturing and logistics. The demand for high-quality parts generated by BMW’s production stimulates growth in the automotive parts sector. The intricate supply chain, encompassing component suppliers, logistics providers, and associated businesses, benefits from BMW’s presence. These related industries experience increased production, employment, and revenue, thus demonstrating the interconnectedness of the US economy. Furthermore, the innovation and technological advancements in the automotive industry are often spurred by the demands of major manufacturers like BMW.
Economic Contribution Summary
The following table illustrates the economic contribution of BMW’s US manufacturing operations, encompassing jobs, investment, and generated revenue. These figures represent a snapshot of the company’s significant impact.
Economic Indicator | Value |
---|---|
Jobs Created (Direct & Indirect) | [Insert Value Here – verifiable source needed] |
Investment in US Facilities | [Insert Value Here – verifiable source needed] |
Revenue Generated | [Insert Value Here – verifiable source needed] |
Future of BMW USA Production
BMW’s US manufacturing footprint is poised for significant evolution, driven by a confluence of factors including market demand, technological advancements, and global economic shifts. The company’s commitment to the American market, coupled with the strategic importance of the US as a production and sales hub, suggests continued investment and adaptation. This section examines potential future expansion plans, factors influencing these plans, and the evolving role of electric vehicles in shaping the future of BMW USA production.
Potential Future Expansion Plans
BMW’s continued presence in the US is likely to include expansion in existing facilities or the establishment of new ones. The rationale behind this stems from the substantial market demand for BMW vehicles in North America, and the desire to optimize production and logistics within the region. Furthermore, the potential for export from these facilities to other markets, particularly in the Americas, underscores the strategic importance of this investment. Existing facilities may be retooled or expanded to accommodate new models, particularly those focusing on electric vehicle production.
Factors Driving or Hindering Expansion
Several factors influence potential expansion plans. Strong consumer demand for luxury vehicles, including BMW’s models, is a significant driver. Government incentives for electric vehicle adoption and infrastructure development can also play a pivotal role. However, rising labor costs, material price volatility, and global economic uncertainties could act as potential obstacles. Furthermore, the increasing complexity of electric vehicle manufacturing, with its associated demands for specialized equipment and skilled labor, presents a unique challenge.
Role of Electric Vehicles in Future Production
Electric vehicles (EVs) are a crucial component of BMW’s future strategy, and this will significantly impact production in the US. The anticipated shift towards EVs necessitates significant investments in retooling existing facilities and potentially establishing dedicated EV production lines. BMW’s experience with other markets, where EV adoption has been more rapid, provides a valuable blueprint for adapting manufacturing processes and integrating new technologies. The company may also explore partnerships with battery manufacturers to secure a reliable supply chain for EV production in the US.
Potential Changes in Manufacturing Processes and Technologies
Future BMW manufacturing will likely incorporate advanced technologies such as automation and robotics. This is essential to increase production efficiency and enhance quality control, particularly as the complexity of EVs increases. 3D printing and other additive manufacturing techniques may also find applications in prototyping and producing specific components, especially in the customization of models. The integration of Industry 4.0 principles, such as data analytics and real-time monitoring, is anticipated to enhance decision-making and improve overall production efficiency.
Potential Future BMW USA Manufacturing Plant
A hypothetical future BMW USA manufacturing plant would likely feature state-of-the-art facilities, incorporating advanced technologies and automation systems. Emphasis would be placed on sustainable practices, including energy efficiency measures and responsible waste management. The plant’s design would prioritize flexibility, allowing for the seamless transition to new models and technologies, such as the integration of electric vehicle production lines. It would be strategically located to optimize logistics and distribution networks, minimizing transportation costs and maximizing efficiency in reaching the target consumer base. This plant would be a model of modern, environmentally conscious, and technologically advanced automotive manufacturing.
Comparison with Other Automotive Manufacturers
BMW’s US production strategy stands in a complex landscape alongside other major automotive manufacturers. The approach to sourcing, manufacturing, and market positioning varies significantly, reflecting differing priorities and competitive pressures. Understanding these nuances is crucial for analyzing the overall health and future trajectory of the US automotive industry.
Comparative Analysis of US Production Strategies
A comparative analysis reveals key similarities and differences in the US production strategies of major automotive manufacturers. Factors influencing these variations include brand identity, product portfolio, supply chain resilience, and market share aspirations. Different approaches to localization, automation, and labor relations also play a significant role.
BMW | Ford | Comparison Point |
---|---|---|
Focuses on premium vehicles and high-end technologies. Extensive use of automation and specialized manufacturing processes. | Offers a broader range of vehicle types, including trucks and SUVs. Emphasizes cost-effectiveness and mass production. | Product Focus and Manufacturing Approach |
Strong emphasis on environmental sustainability and efficiency in manufacturing processes. Primarily relies on advanced materials and technologies. | Historically focused on efficiency, but increasingly emphasizing sustainability initiatives. Leverages existing manufacturing infrastructure. | Environmental Sustainability and Technology |
Significant investment in research and development, with a strong emphasis on innovation. Prioritizes high-quality components and materials. | Significant investment in R&D, but often prioritizing cost-effectiveness and efficiency. Prioritizes reliability and durability. | Innovation and Quality Standards |
Supply chain is diversified but reliant on key partnerships. May face challenges with geopolitical uncertainties. | Extensive and complex supply chain, susceptible to disruptions. Seeks to diversify sourcing to mitigate risks. | Supply Chain Resilience |
BMW | Toyota | Comparison Point |
---|---|---|
Primarily focused on luxury vehicles and performance-oriented models. Sophisticated manufacturing techniques and high-quality materials. | Offers a wide range of vehicles, with a strong presence in both mass-market and luxury segments. Known for lean manufacturing and efficiency. | Product Focus and Manufacturing Approach |
High level of integration between design, engineering, and manufacturing. Emphasizes advanced technologies and premium features. | Emphasizes streamlined production processes and reduced waste. Leverages efficient supply chain management. | Manufacturing Process and Efficiency |
Significant investments in alternative powertrains, aiming for sustainable mobility. Highly specialized manufacturing facilities. | Progressively embracing alternative powertrains, with a focus on hybrid and electric vehicles. Leverages extensive manufacturing experience. | Technological Advancements and Sustainability |
Strong emphasis on design aesthetics and brand image. Premium pricing strategy. | Prioritizes reliability, fuel efficiency, and affordability. Competitive pricing strategy. | Brand Image and Market Positioning |
Factors Influencing Differences
The differences in production strategies arise from several factors. Different manufacturers prioritize different aspects of the automotive industry. For example, some companies may focus on mass production, while others prioritize premium features and brand image. The specific technological capabilities of each company also significantly affect its choices regarding automation, material sourcing, and supply chain management. Finally, the competitive landscape in the US automotive market plays a significant role in shaping each manufacturer’s approach to production and distribution.
Competitive Landscape in the US Automotive Market
The US automotive market is highly competitive, with established players like Ford, GM, and Toyota facing challenges from new entrants and evolving consumer preferences. The market is increasingly influenced by environmental regulations, consumer demand for electric vehicles, and global economic uncertainties. These factors necessitate a dynamic and adaptable approach to manufacturing and distribution.
Environmental Considerations
BMW’s US manufacturing operations are increasingly focused on minimizing their environmental impact. The company recognizes the crucial role it plays in reducing its carbon footprint and promoting sustainable practices throughout its supply chain and manufacturing processes. This commitment extends beyond compliance with regulations to encompass proactive initiatives aimed at reducing emissions, conserving resources, and promoting circularity.
Environmental Impact of BMW’s US Manufacturing
BMW’s US manufacturing facilities, like other large-scale industrial operations, contribute to greenhouse gas emissions. These emissions stem from energy consumption during manufacturing processes, transportation of materials, and waste disposal. However, the company actively measures and monitors these impacts to understand areas for improvement and implement sustainable solutions. Reducing the environmental impact requires careful analysis of each stage of the production process.
Sustainability Initiatives and Practices
BMW’s commitment to sustainability is evident in its adoption of various initiatives. These initiatives are designed to minimize environmental damage while maximizing resource efficiency and minimizing waste. The company’s comprehensive approach encompasses the entire lifecycle of its vehicles, from material sourcing to end-of-life management.
Eco-Friendly Measures Employed
BMW employs several eco-friendly measures across its US manufacturing facilities. These measures include:
- Optimized Energy Efficiency: BMW utilizes advanced technologies and energy-efficient equipment to reduce energy consumption in its manufacturing processes. This includes implementing energy-saving strategies like improved insulation and smart lighting systems to lower energy usage and emissions.
- Waste Reduction and Recycling: BMW prioritizes waste reduction and recycling throughout its operations. They implement programs to minimize waste generation by optimizing processes and implementing comprehensive recycling programs for various materials used in production.
- Sustainable Sourcing: BMW emphasizes the sustainable sourcing of raw materials. The company partners with suppliers committed to environmentally responsible practices, ensuring that materials used in production meet stringent sustainability criteria. This commitment extends to the supply chain, aiming to minimize the environmental impact throughout the entire lifecycle of the vehicle.
Commitment to Reducing Carbon Footprint
BMW actively strives to reduce its carbon footprint by implementing strategies across various stages of production. These strategies include:
- Investing in Renewable Energy: BMW is progressively transitioning to renewable energy sources, such as solar power, to power its facilities. This move aims to reduce reliance on fossil fuels and lessen the carbon emissions associated with electricity generation. The company aims to maximize the use of renewable energy sources in its manufacturing processes.
- Emissions Monitoring and Reduction: BMW employs sophisticated systems to track and monitor greenhouse gas emissions. These systems allow the company to identify areas for improvement and implement strategies to reduce emissions across all manufacturing stages. This data-driven approach helps BMW track progress and make informed decisions for reducing emissions.
Use of Recycled Materials and Renewable Energy Sources
BMW is increasingly incorporating recycled materials into its vehicle production. This includes:
- Recycled Plastics and Metals: BMW actively utilizes recycled plastics and metals in various vehicle components. The company aims to increase the proportion of recycled materials in its production, contributing to a more circular economy.
- Renewable Energy Integration: The integration of renewable energy sources, such as solar panels and wind turbines, reduces reliance on traditional energy sources. BMW’s commitment to using renewable energy is demonstrated through its investments in renewable energy infrastructure.