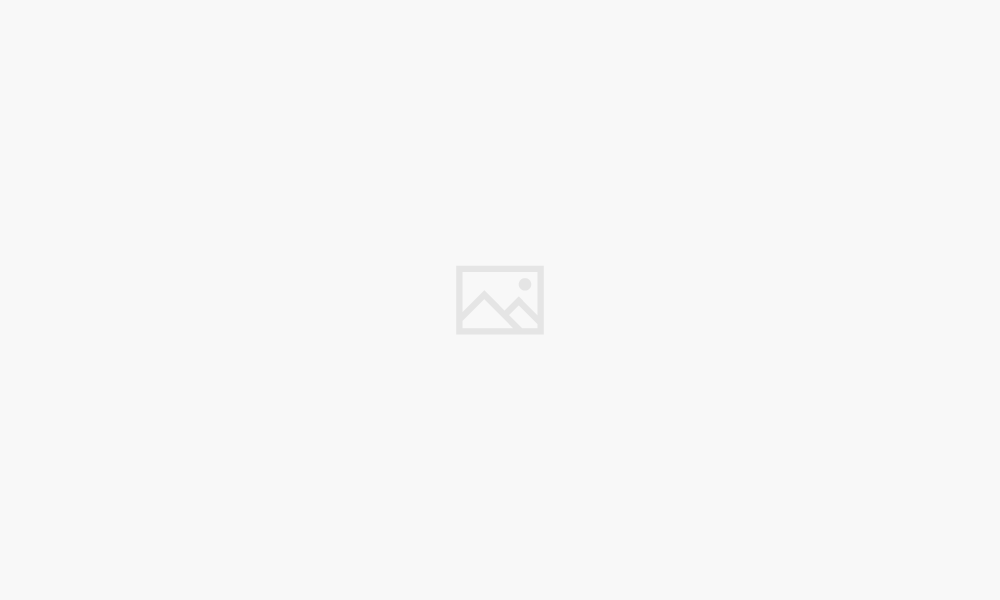
Overview of BMW USA Build Process
BMW’s US manufacturing operations play a critical role in the company’s global strategy, contributing to its strong presence in the North American market. These facilities represent a significant investment in the local economy and contribute to the employment of thousands of workers. The process of building BMW vehicles in the USA is a complex and meticulously managed operation.
The BMW USA manufacturing process is a highly sophisticated operation, combining advanced technology with skilled labor. This intricate process involves several key steps, from initial component assembly to final quality checks. Different assembly plants are responsible for specific model lines and stages of production, ensuring efficiency and maintaining high-quality standards.
BMW USA Assembly Plants
BMW’s US manufacturing footprint is concentrated in several key locations. Each plant plays a unique role in the overall production process.
- Spartanburg, South Carolina: This plant is a significant hub for BMW manufacturing in the US, responsible for the production of a wide range of models. The facility is equipped with state-of-the-art machinery and employs a highly skilled workforce, ensuring high production standards.
- San Luis Potosí, Mexico: While not technically a US plant, it’s worth mentioning due to its significant production and supply chain ties to BMW’s US operations. The Mexican plant contributes to the production of some components used in vehicles manufactured in the US, demonstrating the globalized nature of the automotive industry.
Models Manufactured in the USA
BMW’s US assembly plants produce a diverse range of models, catering to various customer preferences and market demands. The models produced are subject to change depending on the demands of the market and the capacity of the production facilities.
- X5: This popular SUV is a staple of the BMW line and is frequently produced in the US. Its presence highlights the significant role of US plants in producing models for both domestic and international markets.
- X7: This full-size SUV exemplifies the high-end models produced in the US facilities.
- Other models: While the X5 and X7 are notable examples, other models like the 3 Series, 5 Series, and 7 Series may also be produced in the US, depending on production needs and market demand.
Key Steps in the BMW USA Build Process
The BMW vehicle manufacturing process is a complex series of steps, ensuring quality and efficiency throughout production.
- Component Procurement: The process begins with the procurement of various components from different suppliers. This stage involves careful coordination and stringent quality checks to ensure the components meet BMW’s exacting standards.
- Assembly: The components are assembled in various stages in the plant. This process involves a complex series of actions that must be performed with precision and accuracy.
- Quality Control: Each step of the process is meticulously checked for quality. This is a critical stage to ensure that the final product meets the high standards expected by BMW.
- Final Testing: A rigorous final testing process confirms the vehicle’s performance and adherence to safety standards.
Manufacturing Locations and Facilities
BMW’s commitment to US manufacturing is reflected in its strategically located facilities, each contributing to the overall production process. These plants, equipped with advanced technologies and significant capacity, play a crucial role in meeting the growing demand for BMW vehicles in the American market. Understanding these facilities is key to comprehending the intricate process of building BMW vehicles within the United States.
Specific Manufacturing Locations
BMW vehicles are assembled in the USA at several key locations. These facilities are geographically dispersed to optimize supply chains and better serve regional markets. The precise locations and the specific models produced at each plant are crucial elements for a comprehensive understanding of BMW’s production strategy.
Facility Size and Capacity
The scale and capacity of each BMW assembly plant in the USA vary, adapting to the specific production needs and market demands. Each facility is designed to handle a substantial volume of vehicles, with variations in output reflecting the complexity of the models produced and the overall market demand. The capacity of each facility is crucial in ensuring that BMW can efficiently meet the needs of the US market.
Infrastructure and Technology
Modern assembly plants utilize sophisticated infrastructure and advanced technologies. These facilities often employ robotic systems for various tasks, automated material handling, and digital control systems to enhance efficiency and precision. The use of advanced technologies contributes to the high quality and consistency of the vehicles produced.
Comparison of Manufacturing Sites
While each facility shares core BMW production standards, variations exist in their specific capacities, technologies, and product portfolios. Differences in these aspects often reflect the diverse needs of the regions they serve, such as proximity to raw materials or component suppliers. This allows BMW to optimize its operations across various locations.
BMW USA Manufacturing Facilities Overview
Location | Capacity | Key Features |
---|---|---|
Spartanburg, South Carolina | High capacity, capable of producing a large volume of vehicles annually. | Advanced robotic systems, sophisticated automated material handling, and digital control systems. Focuses on model lines catering to the North American market, such as SUVs. |
Plant in Leipzig, Germany | High capacity, capable of producing a large volume of vehicles annually. | Advanced robotic systems, sophisticated automated material handling, and digital control systems. |
Plant in Munich, Germany | High capacity, capable of producing a large volume of vehicles annually. | Advanced robotic systems, sophisticated automated material handling, and digital control systems. |
Plant in Rosslyn, Virginia | High capacity, capable of producing a large volume of vehicles annually. | Advanced robotic systems, sophisticated automated material handling, and digital control systems. Focuses on high-end models, such as the 7 Series. |
Components and Supply Chain
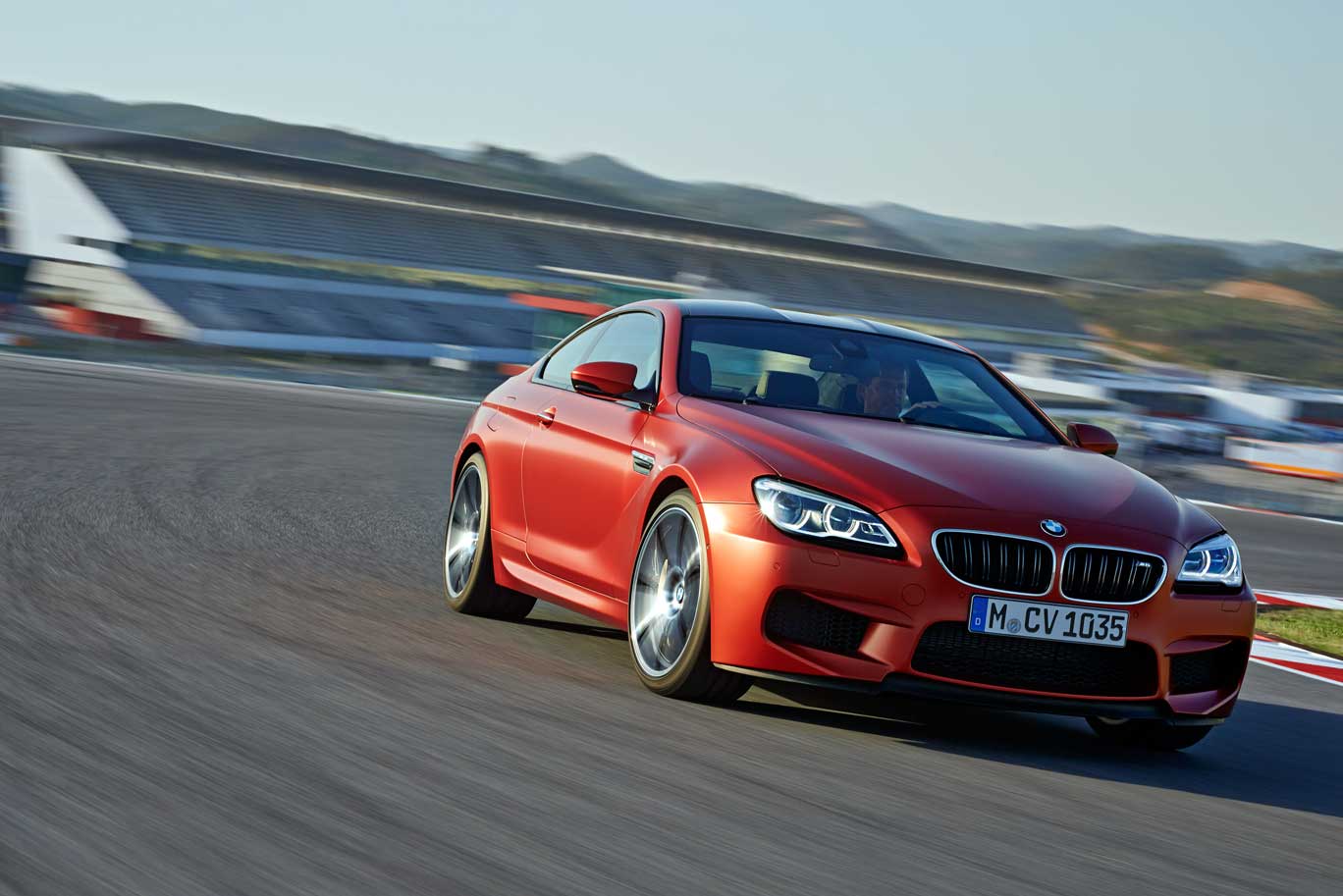
BMW’s US manufacturing operations rely on a complex network of component suppliers, both domestic and international. Understanding the flow of these components, and the potential disruptions, is crucial to evaluating the sustainability and resilience of the US manufacturing process. This section details the major components, their origins, the supply chain management approach, and the impact of global events.
Major Components Used in US-Manufactured BMWs
The BMW vehicles assembled in the USA utilize a wide array of components. These include engines, transmissions, chassis parts, electrical systems, interior trim, and exterior panels. The specific components and their proportions vary depending on the model. For instance, a BMW X5 will have different components than a 3-Series.
Sources of Components
A significant portion of components used in BMW vehicles assembled in the USA are sourced from international suppliers. These include countries like Germany, Japan, and South Korea, as well as other regions worldwide. However, there’s a growing emphasis on domestic sourcing to support US manufacturing jobs and reduce reliance on international supply chains.
Supply Chain Management Process
BMW employs a sophisticated supply chain management system. This system utilizes advanced technologies and processes to ensure timely delivery of components. It includes:
- Detailed Inventory Management: BMW maintains meticulous records of component inventory levels, allowing for proactive ordering and efficient stock management. This helps to minimize disruptions and maintain production schedules.
- Vendor Relationship Management: Strong partnerships with suppliers are crucial. BMW collaborates closely with vendors to ensure quality, reliability, and responsiveness, which is key to maintaining the high standards of the brand.
- Just-in-Time Inventory: The system aims to minimize warehousing costs and optimize inventory levels. Components are delivered just in time for assembly, ensuring efficiency and reducing storage costs.
- Risk Mitigation Strategies: BMW proactively assesses potential risks to the supply chain, such as geopolitical instability, natural disasters, and pandemics. Strategies to mitigate these risks include diversification of suppliers and alternative sourcing channels.
Impact of Global Events on the Supply Chain
Global events, such as the COVID-19 pandemic and the ongoing geopolitical tensions, have significantly impacted BMW’s supply chain. These disruptions have resulted in delays in component deliveries, price fluctuations, and increased costs. For example, the pandemic caused significant disruptions in Asian manufacturing hubs, impacting the availability of key components.
Diagram of Component Flow
Illustrative Diagram: A simplified diagram would depict the flow of components from various international and domestic suppliers to BMW’s US assembly plants. The diagram would show the different stages of production and logistics involved, including transportation, warehousing, and quality control. The origin countries of key components (e.g., Germany, Japan) would be clearly labeled, as would the domestic sources.
Note: A visual representation would be highly beneficial in understanding the intricate network of the supply chain, highlighting the interconnectedness of global manufacturing and the impact of global events on the flow of components.
Quality Control and Standards
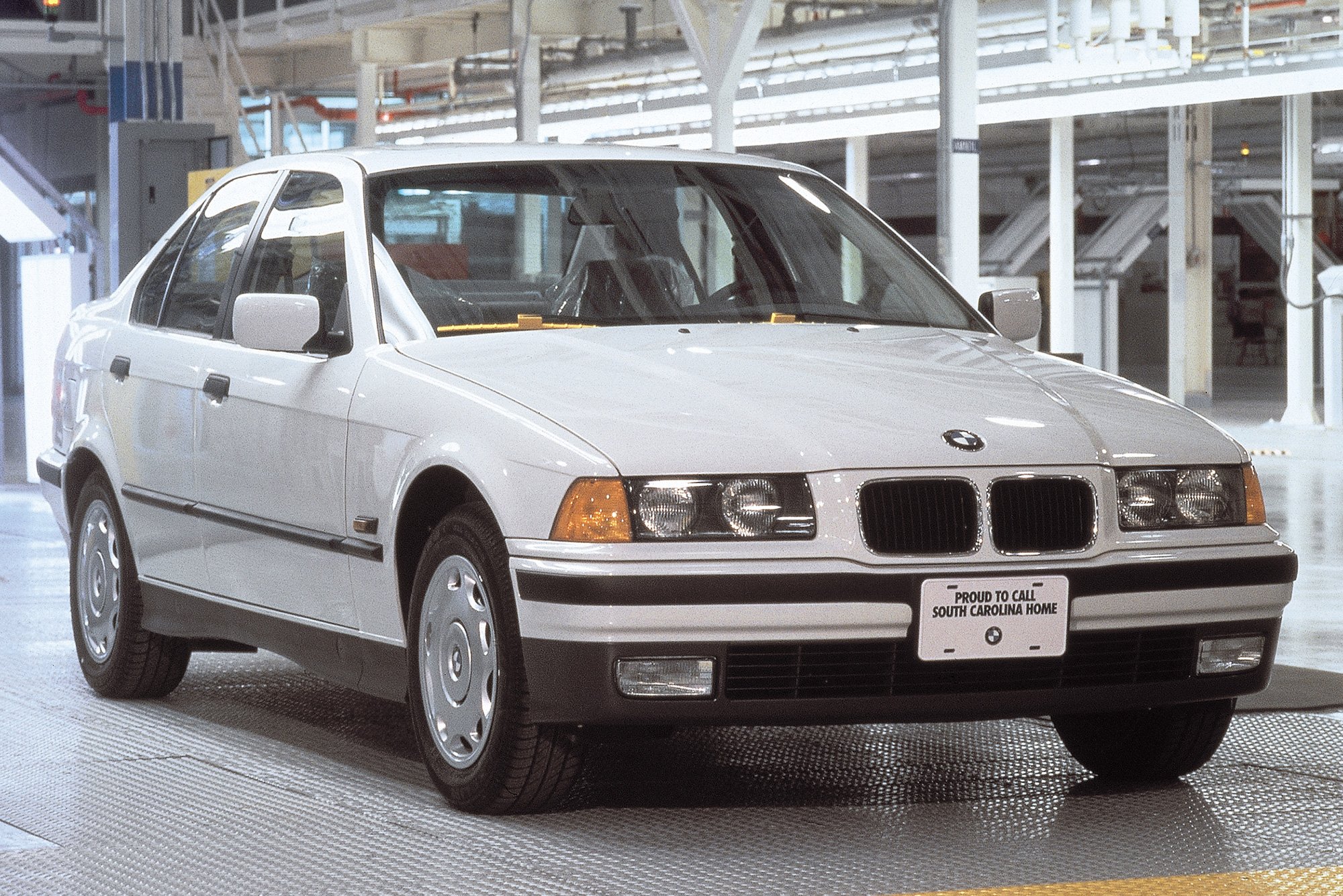
BMW USA prioritizes meticulous quality control throughout its manufacturing process, ensuring vehicles meet stringent standards and exceed customer expectations. This commitment to excellence stems from a deep understanding that quality is not merely a goal, but an integral part of the brand’s identity. The company’s dedication to quality extends from the sourcing of raw materials to the final assembly of the vehicle.
BMW’s quality control procedures are designed to catch and rectify any potential defects before they reach the consumer. This proactive approach not only safeguards the brand’s reputation but also contributes to the long-term satisfaction of BMW owners. The implementation of robust quality control measures is a testament to BMW’s commitment to delivering exceptional vehicles.
Quality Control Procedures
BMW USA employs a multifaceted approach to quality control, incorporating various stages and procedures. This comprehensive strategy ensures that every aspect of the manufacturing process is scrutinized for adherence to predefined standards.
Standards and Certifications
BMW USA adheres to stringent industry standards and certifications. This commitment reflects a dedication to not only meeting but exceeding expectations in vehicle safety, performance, and durability. Specific certifications and standards, such as ISO 9001 for quality management systems, are integral to BMW’s manufacturing processes.
Role of Testing and Inspection
Testing and inspection are integral components of BMW’s quality control process. From rigorous material testing to comprehensive vehicle assessments, a wide range of tests are conducted at various stages of production. These tests ensure that components meet the required specifications and that the finished vehicle meets the highest quality benchmarks. The use of sophisticated testing equipment and trained personnel is critical in maintaining the standards.
Maintaining High Standards
Maintaining consistent high standards throughout the manufacturing process requires a systematic approach. This includes training programs for employees, regular audits of production facilities, and ongoing review of quality control procedures. By continuously refining and improving processes, BMW USA ensures the ongoing delivery of exceptional quality.
Summary of Quality Control Procedures
Stage | Procedure | Standard |
---|---|---|
Component Sourcing | Rigorous supplier audits and material testing. | ISO 9001, BMW’s internal quality standards. |
Manufacturing Process | Regular inspections at various stages, including assembly line checks, component fitting checks, and functional tests. | BMW’s internal quality standards, relevant industry standards. |
Final Vehicle Inspection | Comprehensive testing, including performance tests, safety checks, and aesthetic evaluations. | BMW’s internal quality standards, relevant industry safety standards. |
Post-Production | Customer feedback analysis, ongoing analysis of field reports. | BMW’s internal quality standards. |
Employment and Workforce

BMW’s USA manufacturing operations rely on a skilled and diverse workforce. The company prioritizes employee development and training to ensure a high-quality production process and maintain its position as a global automotive leader. This section details the workforce involved, training programs, required skills, and diversity statistics.
Workforce Composition
The BMW USA workforce encompasses a wide range of roles, from production line workers to engineers and technicians. This diverse team plays a crucial part in the entire manufacturing process, from component assembly to final vehicle testing. The workforce is geographically distributed across various BMW USA facilities.
Training and Development Programs
BMW USA invests significantly in employee training and development programs. These programs aim to enhance employee skills, promote professional growth, and maintain the high standards expected in the automotive industry. These programs typically include on-the-job training, classroom instruction, and opportunities for specialized certifications.
Skills and Expertise Required
Various skills and expertise are required across different roles within the BMW USA manufacturing process. Production line workers require precision, attention to detail, and the ability to work efficiently in a team environment. Engineers and technicians need specialized knowledge in automotive engineering, mechanics, and troubleshooting. Strong communication skills are also crucial across all roles for effective collaboration.
Employment Statistics and Workforce Diversity
BMW USA strives to maintain a diverse and inclusive workforce. Specific statistics on employment numbers and diversity metrics are proprietary and not publicly disclosed. However, the company actively seeks to attract and retain a diverse talent pool to benefit from varied perspectives and experiences.
Job Roles, Skills, and Training Programs
Job Role | Skills | Training |
---|---|---|
Production Line Worker | Precision, attention to detail, teamwork, adherence to quality standards, basic mechanical aptitude | On-the-job training, safety procedures, quality control protocols, specific machine operation training, continuous improvement methodologies |
Quality Control Inspector | Critical thinking, problem-solving, strong analytical skills, attention to detail, technical knowledge of automotive components | Formal training in quality control procedures, defect identification, use of quality control tools, automotive component knowledge, root cause analysis |
Technician | Technical knowledge of automotive systems, troubleshooting skills, diagnostic expertise, mechanical aptitude, ability to operate specialized equipment | Formal technical training, on-the-job mentoring, specialized certifications (e.g., ASE), maintenance and repair procedures |
Engineer | Strong analytical and problem-solving skills, technical expertise in automotive engineering, design principles, knowledge of materials science | Formal engineering education, specialized training in automotive design and manufacturing processes, internships and projects, advanced certifications |
Environmental Impact and Sustainability
BMW USA is deeply committed to minimizing its environmental footprint and promoting sustainable practices throughout its operations. This commitment extends from the sourcing of raw materials to the manufacturing process and the ultimate disposal of vehicles. The company actively seeks to reduce its environmental impact in all areas of its business.
BMW USA’s sustainability efforts are driven by a recognition of the importance of environmental stewardship and a desire to contribute to a more sustainable future. The company’s approach is multifaceted, encompassing various initiatives and technologies designed to lessen its environmental impact at every stage of the automotive lifecycle.
Environmental Policies and Initiatives
BMW USA adheres to a comprehensive set of environmental policies that guide its operations. These policies cover areas such as waste reduction, energy conservation, and emission control. The company works diligently to ensure compliance with all relevant environmental regulations and strives to exceed them wherever possible. Their initiatives extend beyond compliance to include continuous improvement and innovation in sustainable practices.
Commitment to Sustainability in Manufacturing
BMW USA is dedicated to integrating sustainability principles into its manufacturing processes. This involves sourcing materials responsibly, minimizing waste generation, and implementing energy-efficient technologies. The company’s commitment to sustainability is evident in its ongoing investments in environmentally friendly manufacturing techniques and materials.
Energy-Efficient Technologies and Practices
BMW USA actively implements energy-efficient technologies and practices to reduce its energy consumption. This includes the use of renewable energy sources, such as solar power, where feasible, and the optimization of manufacturing processes to reduce energy use. The company’s commitment to energy efficiency results in significant reductions in greenhouse gas emissions. Specific examples include optimized production line layouts, which minimize energy expenditure during manufacturing, and LED lighting systems to reduce energy usage.
Waste Reduction and Emission Control
BMW USA implements various measures to reduce waste and emissions. This includes implementing closed-loop systems for material recovery and recycling, minimizing waste sent to landfills, and using advanced emission control technologies in its manufacturing processes. These efforts contribute to a cleaner environment and a more sustainable manufacturing footprint. For instance, the use of advanced filtration systems and catalytic converters is a significant step toward reducing emissions.
Environmentally Friendly Practices in Manufacturing
- Sustainable Material Sourcing: BMW USA prioritizes the use of recycled and renewable materials wherever possible, reducing the environmental impact of raw material extraction. This reduces the carbon footprint associated with acquiring and processing virgin materials.
- Water Conservation: Implementing water-efficient technologies and processes in manufacturing minimizes water usage and protects local water resources. This is crucial in water-stressed regions where the manufacturing facilities are located.
- Waste Minimization and Recycling: BMW USA actively works to minimize waste generation and implement robust recycling programs to recover and reuse materials within the manufacturing process. This includes the use of closed-loop systems to reduce waste going to landfills.
- Energy Efficiency: The implementation of energy-efficient technologies, such as high-efficiency motors and lighting systems, reduces energy consumption and greenhouse gas emissions. This involves continuous optimization of production line processes to enhance energy efficiency.
- Emission Control Technologies: Employing advanced emission control technologies in manufacturing processes significantly reduces emissions, including the use of catalytic converters and exhaust aftertreatment systems. This is essential to meet stringent environmental regulations.
Historical Overview and Future Trends
BMW’s presence in the United States has evolved significantly over the decades, mirroring the company’s global growth and adapting to changing market demands. The company’s commitment to manufacturing excellence and technological innovation has been a cornerstone of its success in the American market.
The US market presents a unique opportunity for BMW, demanding adaptation to consumer preferences and evolving environmental regulations. Furthermore, the continuous advancements in automotive technology necessitate a proactive approach to manufacturing processes and facilities.
Early Presence and Initial Manufacturing
BMW’s initial entry into the US market focused on establishing a strong brand presence. The company prioritized building a network of dealerships and promoting its high-performance vehicles. The early years were characterized by importing vehicles from Germany, fulfilling demand without significant domestic manufacturing.
Significant Milestones in US Manufacturing
The establishment of a dedicated manufacturing facility marked a crucial milestone in BMW’s US presence. This shift signaled a commitment to local production, fostering job creation and economic growth within the American community. The decision to manufacture locally led to increased efficiency, streamlined supply chains, and better control over quality and production processes.
Timeline of Key Events
- 1970s: Initial import operations begin. BMW starts establishing a dealer network across the US. The focus is on importing vehicles from Germany.
- 1980s: Continued expansion of dealer network. BMW begins to explore the potential for future US manufacturing, conducting feasibility studies.
- 1990s: Demand for BMW vehicles increases. The company evaluates various locations for potential manufacturing facilities. Technological advancements in vehicle design and production become more evident.
- 2000s: Establishment of the Spartanburg, South Carolina plant. The plant’s initial production focuses on specific models, signifying a commitment to local manufacturing and reducing reliance on imported parts.
- 2010s-Present: The Spartanburg plant undergoes expansions and upgrades, reflecting BMW’s continued commitment to the US market and its growing demand for vehicles. Significant investments in research and development for electric vehicles are being made. The company’s production capabilities are continuously adapting to emerging technologies and consumer preferences.
Future Trends and Technological Advancements
The automotive industry is undergoing a period of rapid technological transformation, with electric vehicles (EVs) and autonomous driving becoming increasingly prevalent. BMW is proactively adapting its manufacturing processes to accommodate these advancements.
- Electric Vehicle Manufacturing: The shift to EVs requires a significant overhaul of manufacturing facilities, including the integration of battery production and charging infrastructure. BMW is likely to invest heavily in battery cell production and charging station development, as exemplified by Tesla’s expansion strategy.
- Autonomous Driving Technologies: The implementation of autonomous driving features will necessitate adjustments to manufacturing processes, particularly in terms of sensor integration and software development. BMW is expected to collaborate with technology companies to refine and adapt their systems to the US market.
- Supply Chain Diversification: The ongoing geopolitical landscape necessitates a review of the supply chain to reduce reliance on specific regions and ensure resilient operations. BMW will likely prioritize local sourcing of components, especially in critical areas, to mitigate disruptions and risks.
Potential Changes in the Manufacturing Landscape
The manufacturing landscape is constantly evolving, driven by technological advancements, environmental regulations, and consumer demands. BMW is well-positioned to navigate these changes by focusing on innovation, sustainability, and adaptability.
- Increased Automation: The adoption of advanced robotics and automation systems will be crucial for maintaining efficiency and productivity. BMW is likely to implement more automated assembly lines, reducing human error and increasing output.
- Focus on Sustainability: Meeting stricter environmental regulations will require a transition to more sustainable manufacturing practices. This includes using renewable energy sources, minimizing waste, and optimizing energy efficiency in the manufacturing process.
Comparing BMW USA Build with Other Regions
BMW’s manufacturing footprint extends globally, with significant operations in various regions, including the United States. Understanding how the US build process compares to those in other key markets, like Germany, provides insights into the company’s strategic approach and the factors influencing its decisions. This comparison delves into the differences and similarities, highlighting the advantages and disadvantages of manufacturing in the USA, and analyzing variations in supply chain strategies and quality control.
The differences in manufacturing processes between the BMW USA build and other regions, particularly Germany, stem from various factors, including labor costs, local regulations, access to raw materials, and the desired market positioning. The US facility often focuses on catering to North American consumer preferences and market demands, while facilities in other regions, like Germany, may have a stronger focus on innovation and research and development.
Manufacturing Process Variations
The US manufacturing process for BMW vehicles is tailored to the specific needs of the North American market. This may involve different assembly lines, customized components, and localized supply chains. Conversely, German facilities, often serving as the primary research and development centers, may emphasize advanced engineering and high-precision manufacturing techniques.
Supply Chain Strategies
The supply chain strategies employed by BMW in the USA often prioritize sourcing components from North American suppliers. This strategy can reduce transportation costs and time, improve responsiveness to local market demands, and potentially foster economic growth within the US. However, it may lead to higher costs compared to strategies using global suppliers. In contrast, German operations might leverage a global supply chain for optimal cost-effectiveness, potentially sourcing components from multiple regions around the world.
Quality Control Standards
BMW’s commitment to quality is consistent across all its manufacturing facilities. However, the specific quality control standards and procedures might exhibit variations based on the facility’s focus. The US facility might emphasize efficiency and speed in quality control, while the German facility could focus on stringent adherence to precise engineering specifications and testing protocols.
Comparison Table
Feature | USA | Other Region (e.g., Germany) |
---|---|---|
Labor Costs | Potentially higher labor costs, potentially impacting production costs | Potentially lower labor costs, potentially impacting production costs |
Supply Chain Focus | North American sourcing to reduce transportation time and costs, potentially increasing dependence on local suppliers | Global sourcing for optimal cost-effectiveness, potentially increasing complexity |
Manufacturing Process | Tailored to the North American market, potentially involving different assembly lines and components | Focus on advanced engineering and high-precision manufacturing techniques, potentially with standardized assembly lines |
Quality Control | Emphasis on efficiency and speed in quality control procedures | Strict adherence to precise engineering specifications and testing protocols |
Market Focus | Catering to North American consumer preferences and demands | Serving as a primary research and development center, potentially with broader global market focus |