Types of Used Car Wash Equipment
Used car wash equipment offers a cost-effective solution for establishing or upgrading a car wash business. The market provides a wide array of options, catering to various budgets and needs, from small-scale operations to large-scale facilities. Understanding the different types of equipment available is crucial for making informed purchasing decisions.
Categorization of Car Wash Equipment
Used car wash equipment can be categorized by its function and application. This allows for efficient selection based on the specific requirements of a car wash operation. Different types of equipment have varying price points and operational features, impacting the overall cost and efficiency of the car wash process.
Pressure Washers
Pressure washers are essential for pre-washing vehicles and removing loose dirt and debris. Their power and water pressure directly influence the effectiveness of the initial cleaning process. Different models offer varying pressure levels, suitable for different cleaning tasks.
Sprayers
Sprayers are crucial for applying cleaning solutions and rinsing vehicles throughout the wash process. The design and nozzle configuration significantly impact the even distribution of cleaning agents. The quality of the sprayer can impact the overall cleanliness and efficiency of the car wash.
Conveyor Systems
Conveyor systems automate the movement of vehicles through the wash bays. They are critical for large-scale operations, increasing throughput and efficiency. The speed and capacity of the conveyor system significantly affect the overall output of the car wash.
Drying Equipment
Drying equipment, such as air blowers and dryers, ensures that vehicles exit the car wash clean and dry. The efficiency of drying equipment contributes to customer satisfaction. The quality and power of the dryers influence the time it takes to dry a vehicle.
Cleaning Chemicals Dispensers
Cleaning chemical dispensers automate the dispensing of cleaning solutions. This precision helps ensure the correct amount of cleaning agent is applied, preventing waste and optimizing the wash process. The accuracy and reliability of the dispensers are crucial for efficiency.
Water Recycling Systems
Water recycling systems reduce water consumption and improve environmental sustainability. These systems significantly decrease water usage and associated costs. Water recycling is crucial for eco-friendly car wash operations.
Table: Types of Used Car Wash Equipment
Equipment Type | Description | Typical Use Cases | Approximate Price Range |
---|---|---|---|
Pressure Washer | High-pressure water jets for initial cleaning. | Pre-washing vehicles, removing loose debris. | $200-$5,000+ |
Sprayer | Applies cleaning solutions and rinses vehicles. | Applying soap, rinsing, and final cleaning. | $100-$2,000+ |
Conveyor System | Automated vehicle movement through the wash bays. | Large-scale car washes, increased throughput. | $1,000-$20,000+ |
Drying Equipment | Removes water from vehicles after washing. | Ensuring vehicles exit clean and dry. | $100-$1,000+ |
Cleaning Chemicals Dispensers | Automated dispensing of cleaning solutions. | Precise application of cleaning agents, reducing waste. | $50-$500+ |
Water Recycling Systems | Reduces water consumption and promotes sustainability. | Eco-friendly car washes, cost savings. | $500-$10,000+ |
Condition and Quality Assessment
Evaluating the condition and quality of used car wash equipment is crucial for making an informed purchase decision. Understanding the different levels of condition, the factors influencing quality, and potential hidden issues can save you significant time and money in the long run. A thorough assessment ensures that the equipment meets your needs and budget while minimizing future maintenance costs.
Condition Ratings
Used car wash equipment can be categorized into various conditions, each affecting its value and potential issues. These ratings are generally used to describe the equipment’s overall state.
- Excellent: Equipment in excellent condition exhibits minimal wear and tear, indicating it has been well-maintained. It typically operates efficiently with few or no issues. Examples include equipment recently upgraded or that has been part of a smaller, more controlled operation, with a documented and regular maintenance schedule.
- Good: Equipment in good condition shows some signs of wear but remains functional and reliable. Normal use may be evident, but the equipment generally operates effectively. This category often includes equipment that has been part of a standard operation for a few years with regular maintenance.
- Fair: Equipment in fair condition displays noticeable wear and tear. It may require minor repairs or adjustments to operate correctly. It may require more maintenance or have a history of some breakdowns.
- Poor: Equipment in poor condition shows extensive wear and tear and may have significant mechanical issues. It likely needs extensive repairs or replacement parts. This category includes equipment with an unclear or undocumented maintenance history, or equipment from a very large and demanding operation.
Factors Affecting Condition
Several factors significantly impact the overall condition of used car wash equipment.
- Age: Older equipment is more likely to have accumulated wear and tear, requiring more maintenance and potentially higher repair costs. The age of the equipment is often a primary factor in the overall quality rating.
- Maintenance History: A well-documented maintenance history provides valuable insights into the equipment’s past performance. Regular maintenance helps prevent major issues and extends the equipment’s lifespan. Lack of maintenance records or an inconsistent maintenance schedule is a significant red flag.
- Wear and Tear: Visible wear and tear, such as scratches, dents, or corrosion, can indicate the equipment’s use history and potential problems. Inspecting these details is important in evaluating the overall quality.
Evaluating Overall Quality
Assessing the overall quality involves a comprehensive evaluation beyond surface appearances.
- Physical Inspection: Carefully inspect the equipment for visible damage, wear patterns, and any signs of previous repairs. Look for leaks, loose connections, and corrosion. This process helps to identify any immediate issues.
- Functional Testing: Test all functions of the equipment to ensure it operates correctly. This includes checking the speed, pressure, and water flow. If possible, have the equipment run for an extended period to uncover potential issues.
- Hidden Issues: Hidden issues like internal component damage or electrical problems might not be immediately apparent. Seek professional inspections or evaluations to identify potential hidden issues that might not be visible at first glance.
Comparing Used Equipment Conditions
This table provides a concise overview of the pros and cons of purchasing used car wash equipment in different conditions.
Condition | Pros | Cons |
---|---|---|
Excellent | High reliability, minimal maintenance, potentially lower repair costs, potentially longer lifespan | Potentially higher purchase price |
Good | Good balance of reliability and cost, reasonable maintenance needs | Potentially some minor repairs required |
Fair | Potentially lower purchase price | Higher maintenance needs, higher risk of unforeseen repairs, potentially shorter lifespan |
Poor | Potentially the lowest purchase price | High repair costs, significant maintenance needs, potential for major breakdowns, significantly shorter lifespan |
Sourcing and Market Trends
Finding the right used car wash equipment often involves navigating a complex market. Understanding the various platforms and current trends can significantly impact your purchase decisions. This section explores common online marketplaces, current market trends, and pricing models to help you make informed choices.
Current market trends and availability of used car wash equipment vary significantly depending on factors such as global economic conditions, the current state of the automotive industry, and specific technological advancements. For example, a downturn in the automotive industry could lead to a surplus of used equipment, potentially impacting pricing. Conversely, a surge in demand for automated car washes could increase the price of used equipment.
Common Online Platforms and Marketplaces
Numerous online platforms and marketplaces facilitate the buying and selling of used car wash equipment. These platforms offer convenient access to a wide range of listings, enabling buyers to compare options and negotiate prices effectively. Major online marketplaces, such as eBay, Craigslist, and specialized industrial equipment marketplaces, provide comprehensive listings. Moreover, industry-specific forums and classifieds can provide valuable leads for particular equipment types.
Market Trends in Used Car Wash Equipment
Several factors influence the used car wash equipment market. The increasing demand for eco-friendly and efficient car washes is driving the market for specialized equipment. This is evident in the rising popularity of water-saving systems and environmentally conscious technologies. Similarly, the trend toward automated car washes continues to drive demand for automated equipment, including conveyor systems and automated spray systems. Moreover, the demand for compact and mobile car wash units is growing, catering to smaller businesses and specific needs.
Pricing Models for Used Car Wash Equipment
The pricing of used car wash equipment is influenced by several factors. These factors include the equipment’s age, condition, brand, model, and functionality. Moreover, market demand and the availability of comparable equipment also play a role.
Platform | Pricing Model | Typical Fees | Comments |
---|---|---|---|
eBay | Auction-based or fixed price | Seller fees, potentially buyer fees | Wide selection but requires careful bidding strategy |
Craigslist | Negotiated price | Generally free, but potential transaction fees | Direct communication with sellers, potential for good deals |
Specialized Industrial Equipment Marketplaces | Fixed price or negotiated price | Transaction fees, potential seller fees | Often focuses on specific equipment types, potentially higher quality |
The table above illustrates the common pricing models employed by different online platforms. These models vary significantly, with auction-based platforms offering potential discounts but requiring careful bidding, while negotiated pricing platforms allow for more direct communication with sellers. The choice of platform will depend on individual needs and preferences.
Maintenance and Repair Considerations
Used car wash equipment, like any machinery, requires ongoing maintenance to ensure optimal performance, longevity, and safety. Neglecting maintenance can lead to costly repairs, decreased efficiency, and potential damage to the equipment itself or surrounding areas. Proper maintenance minimizes downtime and maximizes the return on investment for your used equipment purchase.
Understanding the specific maintenance needs of different types of used car wash equipment is crucial for successful operation. This includes knowing the routine maintenance tasks, the potential repairs that might arise, and the associated costs. By proactively addressing maintenance issues, you can avoid costly breakdowns and maintain a high level of operational efficiency.
Potential Maintenance Needs
Used car wash equipment can exhibit a variety of maintenance needs, ranging from simple tasks to more complex repairs. These needs vary depending on the type of equipment, its age, and the frequency of use. Common issues include wear and tear on mechanical components, such as pumps, motors, and conveyors. Electrical systems can also require attention due to aging wiring, faulty controls, or damaged connections. Water-related issues, like clogs in pipes and filters, and the buildup of debris, can also cause operational problems. Regular inspection and maintenance can help mitigate these issues and prevent more serious problems.
Routine Maintenance Steps
Proper routine maintenance is essential for keeping used car wash equipment functioning optimally. Following a scheduled maintenance plan minimizes unexpected downtime and maximizes the lifespan of the equipment. A well-maintained system reduces the risk of costly repairs and ensures consistent performance.
- Cleaning and Inspection: Regular cleaning of the equipment, including exterior surfaces and internal components, is crucial. This prevents the accumulation of debris, which can lead to blockages and damage. Inspecting all moving parts, seals, and connections for signs of wear and tear is also important.
- Lubrication: Regular lubrication of moving parts, such as bearings and gears, is vital for preventing friction and wear. Following the manufacturer’s recommendations for lubrication frequency and type is essential. This ensures smooth operation and extends the lifespan of the components.
- Fluid Checks and Replacement: Regular checks of hydraulic fluids, transmission fluids, and other critical fluids are essential. Replacing fluids as needed prevents corrosion and ensures proper equipment function. Fluid levels should be checked and maintained according to the manufacturer’s specifications.
- Electrical System Checks: Inspecting electrical connections, wiring, and control systems for any signs of damage or wear is vital. This includes checking for loose connections, frayed wires, or damaged components. Regular checks prevent electrical issues and potential hazards.
Common Repairs
Addressing potential repairs promptly is key to minimizing downtime and preventing more significant issues. Knowing the common repairs for used car wash equipment allows for proactive maintenance and cost savings.
- Pump Malfunctions: Pump failures are a common problem in used car wash equipment. This can involve issues with seals, bearings, or the pump motor itself. These failures can disrupt the entire washing process and need to be addressed promptly.
- Electrical Component Failures: Faulty motors, controls, or wiring can lead to electrical issues, halting the car wash operation. Troubleshooting and replacing faulty components are often necessary.
- Mechanical Component Failures: Wear and tear on conveyors, arms, or other mechanical components can lead to breakdowns. Repairing these issues might require replacing parts or adjusting mechanisms.
- Water System Clogs: Clogs in pipes, filters, or nozzles can severely impact water flow and cleaning efficiency. Addressing these clogs often involves cleaning or replacing the affected parts.
Maintenance Cost Examples
The cost of maintenance can vary significantly depending on the type of equipment and the frequency of use. These estimates are based on average costs in the industry and may vary depending on specific circumstances.
Equipment Type | Routine Maintenance Costs (Annual) | Repair Costs (Per Incident) |
---|---|---|
High-pressure washers | $200-$500 | $100-$1000 |
Conveyor systems | $300-$800 | $200-$2000 |
Drying systems | $150-$400 | $150-$1500 |
Wash arms and brushes | $100-$300 | $50-$500 |
Safety and Operational Aspects
Used car wash equipment, while offering efficient cleaning solutions, presents potential safety and operational hazards if not handled and maintained correctly. Understanding these aspects is crucial for both the safety of personnel and the long-term performance of the equipment. Prioritizing safety protocols and adhering to operational guidelines ensures optimal performance and minimizes the risk of accidents or environmental damage.
Safety Precautions for Handling and Operating Used Car Wash Equipment
Proper handling and operation of used car wash equipment is paramount for preventing accidents and injuries. Ensuring equipment is in a safe operating condition, adhering to manufacturer guidelines, and employing safe work practices are essential. This involves performing pre-operational checks, using appropriate personal protective equipment (PPE), and establishing clear procedures for equipment operation and maintenance.
- Pre-Operational Checks: A thorough inspection before each use is critical. Verify all components are securely fastened, electrical connections are intact, and all moving parts function correctly. Look for any signs of damage or wear that could compromise safety. Any identified issue must be addressed before operation to prevent potential malfunctions or injuries.
- Personal Protective Equipment (PPE): Appropriate PPE, such as safety glasses, gloves, and sturdy footwear, should be worn by all personnel involved in handling or operating the equipment. This protection safeguards against flying debris, chemical splashes, and potential slips or falls, particularly when working around moving parts.
- Clear Operating Procedures: Establishing and strictly adhering to clear operating procedures for each piece of equipment is essential. These procedures should detail the steps involved in starting, stopping, and maintaining the equipment. Training personnel on these procedures before allowing them to operate the equipment is crucial.
Guidelines for Ensuring Proper Functioning and Avoiding Hazards
Maintaining the equipment’s optimal functioning and avoiding potential hazards is critical for preventing accidents and extending the equipment’s lifespan. This involves regular maintenance, adherence to manufacturer specifications, and prompt addressing of any malfunctions. Addressing potential hazards proactively is a vital aspect of this practice.
- Regular Maintenance: Regular maintenance, including lubrication, cleaning, and inspections, helps maintain the equipment’s optimal performance and longevity. Following the manufacturer’s recommended maintenance schedule is critical to preventing breakdowns and ensuring safety.
- Adherence to Manufacturer Specifications: Using the equipment according to the manufacturer’s instructions and specifications is crucial. Deviations from these specifications can lead to malfunction, equipment damage, and safety hazards. Understanding and complying with the instructions in the manuals is a critical safety measure.
- Prompt Addressing of Malfunctions: Any signs of malfunction, such as unusual noises, vibrations, or leaks, should be immediately addressed. Ignoring these signs can lead to more significant issues and potential safety hazards, such as equipment failure or injury. Prompt intervention is essential.
Environmental Impact of Different Types of Used Car Wash Equipment
The environmental impact of used car wash equipment varies based on the equipment’s design and operational practices. Assessing and mitigating the environmental footprint of these machines is a crucial aspect of responsible operation. Consideration of water usage, chemical consumption, and waste disposal procedures is vital for minimizing negative impacts.
- Water Consumption: Some car wash systems use significantly more water than others. Choosing equipment with water-saving features can reduce the environmental impact. Implementing water recycling systems can further minimize the water footprint of the operation.
- Chemical Usage: The type and amount of chemicals used in car washes can affect the environment. Opting for eco-friendly or biodegradable cleaning solutions can reduce the environmental impact. Proper chemical storage and disposal procedures are crucial.
- Waste Disposal: Proper disposal of used cleaning solutions and other waste materials is critical. Following local regulations and using appropriate waste disposal methods is vital for minimizing pollution.
Examples of Safety Procedures and Guidelines for Different Equipment Types
Implementing specific safety procedures and guidelines tailored to different types of used car wash equipment is crucial for mitigating risks. This may involve using specific PPE for certain equipment types, implementing different operational procedures for various equipment, and creating detailed safety checklists for specific tasks.
- High-Pressure Washers: When operating high-pressure washers, ensure that personnel wear safety glasses, ear protection, and appropriate clothing to prevent injury from flying debris or water pressure. Always keep a safe distance from the nozzle during operation. Ensure proper hose connections are made and secured to prevent leaks or hose bursts.
- Automated Car Wash Systems: For automated systems, follow the manufacturer’s guidelines regarding starting, stopping, and servicing the equipment. Be aware of moving parts and ensure that no one is in the equipment’s path during operation. Perform regular inspections to ensure proper operation.
Financing and Budgeting
Securing funding and creating a realistic budget are crucial steps in purchasing and maintaining used car wash equipment. Careful planning minimizes financial risk and maximizes return on investment. A well-defined budget helps in making informed decisions about the equipment’s purchase and long-term operational costs.
Effective financial planning for used car wash equipment acquisition involves exploring various financing options, understanding the projected costs of purchase and maintenance, and comparing these figures to the potential return on investment. This allows business owners to make informed choices that align with their financial goals.
Financing Options for Used Car Wash Equipment
Various financing options are available for acquiring used car wash equipment. These options range from traditional loans to specialized equipment financing programs. Understanding the nuances of each option is critical to selecting the most suitable financing method.
- Bank Loans: Banks offer various loan options for businesses, including those specifically designed for equipment purchases. These loans typically require a thorough credit check and detailed financial projections. Interest rates and loan terms are influenced by the borrower’s creditworthiness and the overall economic climate. For example, a business with a strong credit history and stable revenue stream might qualify for a lower interest rate and longer repayment period.
- Equipment Financing Companies: Specialized equipment financing companies often provide tailored financing solutions for specific types of equipment, including car wash systems. These companies often have streamlined approval processes and can offer flexible repayment options, potentially reducing the administrative burden on the buyer. Examples of such companies may include commercial financing institutions that specialize in equipment acquisition.
- Lease Agreements: Leasing used car wash equipment can be a viable alternative to purchasing. Lease agreements typically involve regular payments for a specific period, without the upfront capital expenditure required for a purchase. Lease terms can be tailored to fit the business’s needs and budget, with options for various durations and payment schedules. However, the total cost of ownership over the lease term may exceed the cost of outright purchase, depending on the lease terms and market conditions.
- Small Business Loans: Small business administration (SBA) loans and other government-backed programs can be helpful for businesses seeking to acquire used car wash equipment. These programs often offer favorable terms and lower interest rates compared to traditional bank loans, especially for startups or businesses with limited financial history. However, eligibility requirements can be stringent and the application process can be more time-consuming.
Budgeting for Used Car Wash Equipment
A realistic budget considers not only the purchase price of the used equipment but also ongoing maintenance and operational costs. Accurate cost projections enable businesses to make sound financial decisions and manage their cash flow effectively.
- Purchase Price: The initial cost of the used equipment is a significant component of the budget. Thoroughly inspect the equipment to determine its true condition and potential repair needs. This will impact the price negotiation process. Consider factors such as the equipment’s age, model, and functionality.
- Maintenance Costs: Regular maintenance is essential to keep used equipment running efficiently and avoid costly repairs. A well-maintained car wash system can significantly reduce the need for extensive repairs, lowering the overall maintenance budget. Estimate costs for routine maintenance, such as lubrication, filter replacements, and component inspections.
- Operational Costs: Factor in electricity consumption, water usage, and labor costs associated with operating the used car wash system. These costs can vary depending on the equipment’s efficiency and the local utility rates.
- Insurance and Taxes: Include insurance costs for the equipment and any applicable taxes in your budget. These costs are often overlooked but can significantly impact the overall financial picture.
Comparing New vs. Used Equipment Costs
The decision between purchasing new or used equipment depends on a variety of factors, including budget, required functionality, and anticipated operational lifespan.
Factor | New Equipment | Used Equipment |
---|---|---|
Initial Cost | Higher | Lower |
Maintenance Costs (Initial) | Lower (typically) | Potentially Higher |
Maintenance Costs (Long-term) | Lower (over the lifespan) | Potentially Higher |
Equipment Functionality | Latest technology and features | May have older technology |
Equipment Reliability | Proven performance | May require additional assessment |
The total cost of ownership (TCO) should be considered when comparing new and used equipment. The TCO includes the initial purchase price, ongoing maintenance costs, operational expenses, and potential repair costs.
Legal and Regulatory Aspects
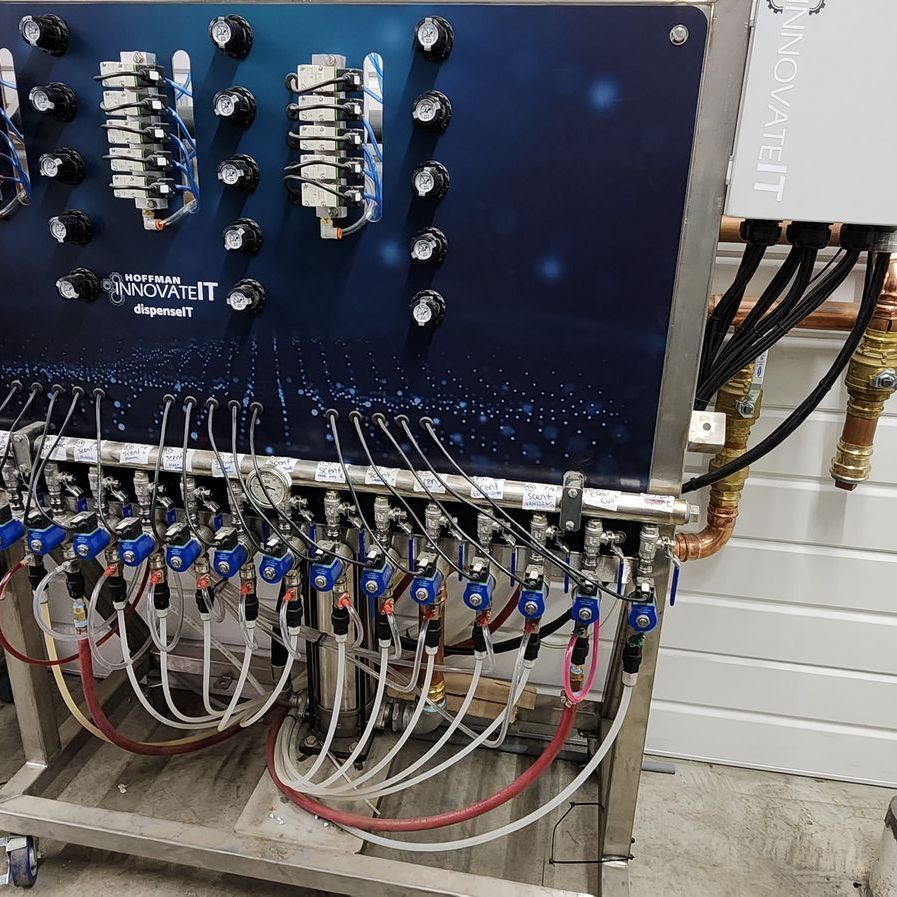
Purchasing used car wash equipment necessitates careful consideration of legal and regulatory requirements. Compliance with safety and environmental regulations is crucial to avoid penalties and ensure a smooth operation. Understanding the legal implications of purchasing used equipment without proper inspection is vital to protect your business interests.
Relevant Legal and Regulatory Requirements
Various local, state, and federal regulations govern the use and operation of car wash equipment. These regulations address safety, environmental protection, and operational procedures. Failure to comply with these regulations can result in significant fines and legal repercussions. Regulations often cover aspects such as wastewater discharge limits, noise pollution levels, and the proper handling and disposal of hazardous materials.
Ensuring Compliance with Safety and Environmental Regulations
Thorough due diligence is paramount to ensure compliance with safety and environmental regulations. This involves verifying that the equipment meets the necessary safety standards and that the disposal of waste materials, such as chemicals and water, adheres to environmental regulations. Inspecting the equipment for compliance with safety standards and environmental regulations is crucial. The inspection should cover aspects like electrical wiring, structural integrity, and the proper functioning of safety mechanisms.
Legal Implications of Buying Used Equipment Without Proper Inspection
Purchasing used car wash equipment without a comprehensive inspection can lead to unforeseen legal and financial problems. A lack of inspection might expose the buyer to potential liability if the equipment malfunctions and causes harm or environmental damage. Without a detailed inspection, you might not discover pre-existing issues that could lead to fines or lawsuits. For example, a faulty electrical system in a used car wash could cause a fire, resulting in legal liabilities for the owner. This emphasizes the importance of a pre-purchase inspection.
Essential Legal Considerations for Purchasing Used Equipment
Legal Consideration | Description |
---|---|
Safety Standards Compliance | Verify the equipment meets relevant safety standards (e.g., electrical codes, mechanical safety features). |
Environmental Regulations | Ensure compliance with wastewater discharge limits, hazardous material handling, and disposal regulations. |
Local Permits and Licenses | Confirm the equipment’s compliance with local permits and licenses for operation. |
Warranty and Maintenance Records | Review any existing warranties and maintenance records to understand the equipment’s past performance and potential issues. |
Transfer of Ownership Documents | Verify proper transfer of ownership and any relevant permits or licenses associated with the equipment. |
Liability Considerations | Understand the potential liabilities associated with equipment malfunction and its impact on your business. |
Seller and Buyer Considerations
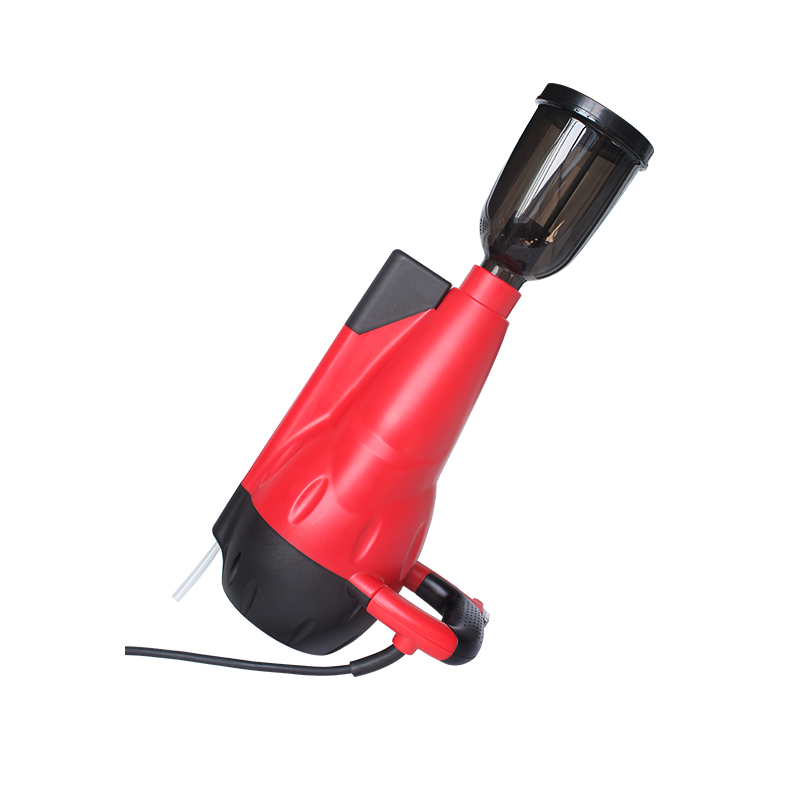
Successfully buying or selling used car wash equipment requires careful planning and attention to detail. Both parties need to understand their respective responsibilities and rights to navigate the process smoothly. Understanding the value proposition and potential pitfalls is crucial for a positive outcome.
Seller Presentation Strategies
Effective presentation of used car wash equipment is paramount to attracting potential buyers. Clear and concise descriptions are essential. Detailed photographs, showcasing the equipment’s condition, are vital. Highlighting any recent maintenance or repairs demonstrates a commitment to quality and care. Providing comprehensive documentation, such as maintenance records, is highly beneficial.
- Thorough Documentation: Maintenance records, repair history, and any relevant permits or certifications should be readily available. This transparency builds trust and provides potential buyers with crucial information.
- High-Quality Photography: Professional photographs showcasing the equipment from various angles are essential. Images should clearly depict the condition of each component, including any signs of wear and tear.
- Accurate Equipment Descriptions: Provide precise details about the equipment’s make, model, age, and any modifications. Highlighting key features, such as water-saving technologies or enhanced cleaning capabilities, can increase buyer interest.
- Competitive Pricing: Research comparable used equipment listings to determine a realistic price point. Consider factors such as the equipment’s age, condition, and market demand.
Buyer Negotiation and Inspection Tactics
Potential buyers should approach negotiations with a strategic mindset. Understanding the market value of the equipment is crucial. A pre-purchase inspection is critical to avoid hidden issues. Thorough documentation of any identified problems during the inspection is essential.
- Market Research: Conduct thorough research on comparable equipment to establish a realistic price range. This will help buyers avoid overpaying.
- Pre-Purchase Inspection: Before committing to a purchase, schedule a comprehensive inspection. A qualified technician can identify potential mechanical issues, structural problems, or hidden damage.
- Detailed Inspection Report: Document all observed conditions during the inspection. This record serves as proof of the equipment’s condition and can be used in case of disputes.
- Negotiation Strategies: Start with a reasonable offer and be prepared to negotiate. Be assertive but respectful during negotiations. Consider offering a slightly lower price in exchange for additional benefits or favorable payment terms.
Seller and Buyer Considerations Summary
This table summarizes key considerations for both sellers and buyers of used car wash equipment.
Category | Seller Considerations | Buyer Considerations |
---|---|---|
Presentation | Provide detailed descriptions, high-quality photos, and maintenance records. | Request a pre-purchase inspection and detailed report. |
Pricing | Research comparable equipment to establish a competitive price. | Research market value to determine a reasonable offer. |
Inspection | Ensure equipment is in good working order and well-maintained. | Thoroughly inspect all components and document findings. |
Documentation | Maintain complete records of maintenance and repairs. | Review all documentation provided by the seller. |
Negotiation | Be flexible and open to negotiation within a reasonable range. | Be prepared to negotiate and offer a fair price. |
Illustrative Examples
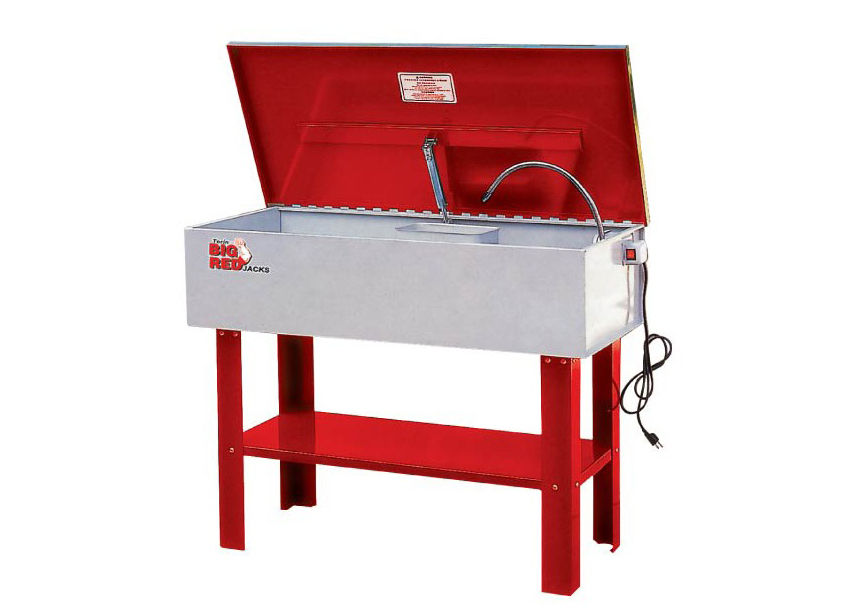
Buying used car wash equipment presents a unique set of considerations, balancing cost-effectiveness with performance and longevity. Understanding these factors is crucial for successful acquisitions. Careful planning, thorough research, and attention to detail are essential throughout the process.
Scenario of Buying Used Car Wash Equipment
A small car wash business owner, aiming to expand their services and attract more customers, is considering purchasing used car wash equipment. They need to wash vehicles faster and more efficiently to meet increased demand. Key steps include evaluating existing equipment, researching available used options, and obtaining vendor recommendations. A detailed budget, including maintenance costs, is essential. Thorough inspections and assessments of the equipment’s condition are paramount. Considering the location and layout of the existing car wash facility and potential future expansion plans are vital in selecting appropriate equipment.
Case Study of a Successful Used Car Wash Equipment Purchase
A car wash business, experiencing high demand, decided to upgrade its equipment. They identified a used high-pressure washer system that met their needs at a fraction of the cost of a new system. The vendor provided a comprehensive inspection report, including maintenance records and a warranty. This report helped the business owner assess the system’s operational history and potential maintenance needs. A trial run of the equipment before purchase further validated its performance and suitability. The business owner, having analyzed several potential used systems, selected one that perfectly aligned with their existing infrastructure and future expansion plans. This strategic decision saved the business significant capital, enabling them to invest in other areas of growth and customer satisfaction.
Scenario of Choosing Used Car Wash Equipment
A business owner is considering adding a foam cannon system to their existing car wash. They need to evaluate their current washing process, assess the type of foam they want to use (chemical or non-chemical), and determine the required water pressure and flow rate. Factors such as budget, space constraints, and the desired level of customer service will influence their choice. Researching various used foam cannon models, comparing their specifications and maintenance requirements, and considering vendor reputation are crucial steps. The business owner must ensure that the chosen equipment aligns with their existing infrastructure and future expansion plans. A comparison of new and used options, taking into account the anticipated lifetime cost of ownership, should be performed.
Illustrative Situations and Considerations
Situation | Considerations | Recommendations |
---|---|---|
Upgrading an existing car wash with limited budget | Identifying used equipment that meets current operational needs and future growth potential, while remaining cost-effective. | Thorough research, comparing multiple options from various vendors, and detailed inspections to identify hidden costs. |
Expanding a car wash business into a new location | Assessing the specific requirements of the new location, including space constraints and water availability, and matching equipment accordingly. | Evaluating used equipment that is suitable for the new location and potential future expansion. Prioritize vendor recommendations and comprehensive reports on the equipment’s history. |
Replacing worn-out equipment to improve efficiency | Identifying used equipment that meets the same or improved performance specifications compared to the existing equipment. | Focusing on reliability and durability of the used equipment, seeking guarantees and warranties, and verifying the equipment’s suitability for the business’s operational demands. |