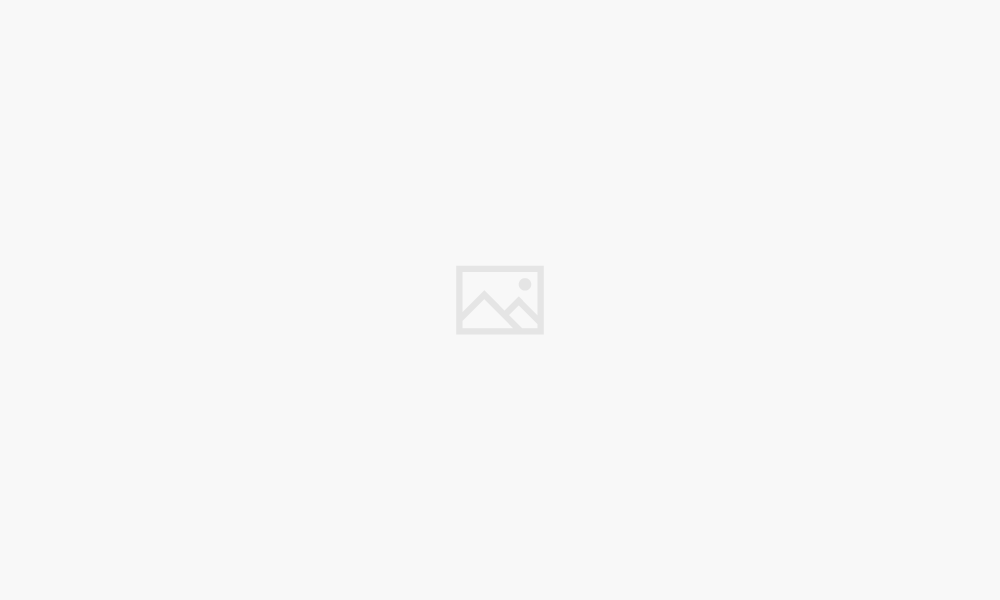
Toyota PMS Overview
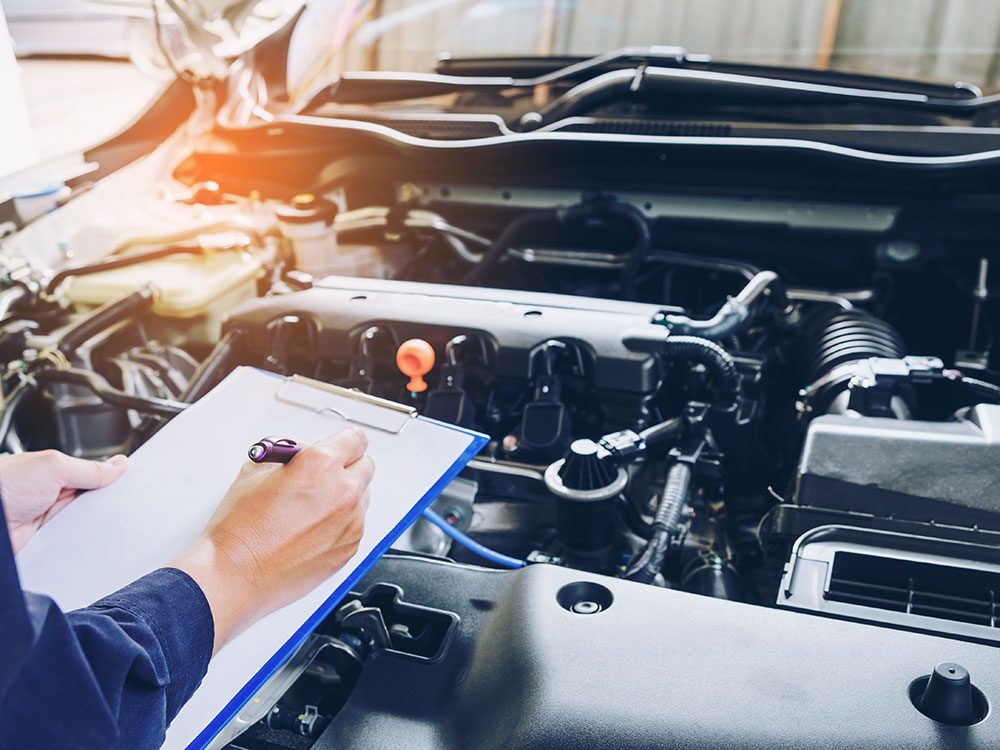
The Toyota Production System (TPS) is a comprehensive manufacturing approach emphasizing efficiency, quality, and continuous improvement. Central to this system is the Toyota Problem Solving Methodology (PMS), a structured framework for identifying, analyzing, and resolving issues within the car production process. This methodology, deeply embedded within Toyota’s organizational culture, plays a critical role in maintaining a high level of quality and efficiency throughout the entire manufacturing lifecycle.
The core principles of TPS, including Just-in-Time (JIT) inventory management, respect for people, and continuous improvement (Kaizen), are fundamental to the effective application of PMS. By fostering a culture of problem-solving and proactive improvement, Toyota aims to minimize waste and maximize value creation at each stage of production.
Key Elements of Toyota Problem Solving Methodology
The Toyota Problem Solving Methodology (PMS) encompasses a structured sequence of steps designed to address production-related challenges. These steps are not merely theoretical but are practically applied throughout the entire manufacturing process, from initial design to final assembly. The methodology focuses on understanding the root cause of problems rather than simply addressing symptoms, ensuring long-term solutions.
Application of PMS in Car Manufacturing Stages
Toyota PMS is deeply integrated into every stage of car production. From the initial design phase, where issues related to component compatibility and manufacturability are identified and resolved, to the final assembly line, where minor defects are swiftly corrected, PMS ensures a seamless flow of production.
- Design Phase: In the design phase, PMS is utilized to identify potential production bottlenecks and design flaws early on. Engineers analyze various design parameters, including material properties, manufacturing processes, and assembly procedures. They meticulously evaluate the design to anticipate and resolve issues before they escalate during production. This proactive approach minimizes the risk of costly rework or delays later in the process. For example, simulations and stress tests are conducted on potential designs to predict potential manufacturing difficulties and design inadequacies.
- Component Production: PMS is critical in maintaining the quality and consistency of components used in car manufacturing. If a component supplier experiences a quality issue, Toyota uses PMS to understand the root cause, implement corrective actions, and ensure future production of that component meets the stringent standards required. This ensures that the components are consistently high quality and meet Toyota’s exacting standards. For instance, if a particular batch of engine parts shows deviations in tolerances, PMS helps pinpoint the source of the issue (e.g., equipment malfunction, raw material inconsistency) and implement a solution.
- Assembly Line: PMS enables quick identification and resolution of assembly-line issues. Toyota employs dedicated problem-solving teams who are trained in PMS methodologies. These teams use structured approaches to investigate issues, such as defects or inefficiencies, on the assembly line. By addressing these issues promptly, they maintain a high level of quality and production efficiency. A clear example would be if a particular car model consistently experiences a specific paint defect, PMS would be used to diagnose the root cause (e.g., incorrect paint application settings) and to implement corrective actions (e.g., adjusting the spray gun settings).
Preventative Maintenance within the Toyota PMS Framework
Preventative maintenance is a cornerstone of the Toyota PMS approach. It emphasizes proactive measures to prevent equipment failures and maintain optimal performance, which minimizes downtime and improves overall production efficiency. This is done by analyzing data to predict potential equipment malfunctions and scheduling maintenance tasks in advance.
- Predictive Maintenance: Toyota uses sophisticated data analysis tools to predict potential equipment failures. This allows for scheduling maintenance tasks before failures occur, reducing unplanned downtime. For instance, monitoring vibration levels and temperature readings of production machinery can help identify potential mechanical issues before they lead to breakdowns. This ensures smooth and continuous production, with minimal disruption.
- Standardized Procedures: Well-defined and standardized maintenance procedures are crucial for consistency and efficiency. By adhering to these procedures, maintenance personnel can consistently perform tasks in the same manner, ensuring optimal performance and minimizing errors. These procedures are meticulously documented and trained to all personnel involved in maintenance.
PMS in Toyota Car Manufacturing
Toyota’s Production Maintenance System (PMS) is a cornerstone of its renowned manufacturing excellence. It’s a comprehensive approach to problem-solving and continuous improvement within the car production process, designed to optimize efficiency, reduce defects, and enhance overall quality. This system goes beyond simple troubleshooting, fostering a proactive culture that anticipates and prevents issues before they arise.
Toyota’s PMS isn’t just a set of procedures; it’s a philosophy ingrained in the company’s culture, emphasizing teamwork, proactive problem identification, and a commitment to constant improvement. This methodology is a critical component of Toyota’s lean manufacturing principles, allowing them to achieve unparalleled levels of efficiency and quality.
Types of Problems Addressed by Toyota PMS
Toyota PMS addresses a wide spectrum of problems encountered in car manufacturing. These include defects in materials, equipment malfunctions, process inefficiencies, and variations in worker performance. The system aims to proactively identify and eliminate these issues at their source, preventing costly and time-consuming rework later in the production line.
Comparison with Other Problem-Solving Methodologies
Compared to other problem-solving methodologies in the automotive industry, Toyota PMS stands out for its emphasis on preventative maintenance and its proactive approach. While other methods might focus on reactive problem resolution, PMS focuses on anticipating potential issues and implementing solutions before they disrupt the production flow. This proactive stance distinguishes Toyota’s approach, allowing for greater efficiency and a reduced likelihood of costly production stoppages.
Key Performance Indicators for Measuring PMS Effectiveness
Several key performance indicators (KPIs) are used to measure the effectiveness of Toyota PMS in car production. These include defect rates, production cycle time, downtime frequency, and the number of corrective actions implemented. Monitoring these KPIs provides a quantifiable assessment of the system’s impact on overall production efficiency. A reduction in these metrics, such as a decrease in defect rates or downtime, directly indicates the success of the PMS.
Fostering Continuous Improvement in Car Manufacturing
Toyota PMS fosters a culture of continuous improvement by encouraging employees at all levels to identify and suggest improvements to manufacturing processes. This participative approach ensures that everyone feels invested in the process and empowers them to contribute to the company’s overall success. The system promotes an environment where employees are not only problem solvers but also active participants in refining the production process, leading to a constant cycle of enhancement.
Steps in a Typical Toyota PMS Problem-Solving Cycle
The Toyota PMS problem-solving cycle is a structured approach that systematically addresses issues. It promotes a collaborative effort among team members to find effective solutions.
Step | Description |
---|---|
Problem Definition | Clearly identifying the problem, its impact, and its root cause through data analysis. |
Data Collection and Analysis | Gathering and analyzing relevant data to understand the problem thoroughly. |
Root Cause Analysis | Identifying the underlying causes of the problem through various techniques such as the 5 Whys. |
Countermeasure Planning | Developing and evaluating potential solutions to address the root cause. |
Implementation | Putting the chosen countermeasure into action, ensuring smooth execution. |
Evaluation and Standardization | Assessing the effectiveness of the implemented solution and establishing standardized procedures to prevent recurrence. |
PMS and Quality Control in Toyota Cars

Toyota’s commitment to producing high-quality vehicles is deeply intertwined with its meticulous Preventive Maintenance System (PMS). The PMS isn’t just a routine maintenance schedule; it’s a comprehensive approach that integrates quality control at every stage of the manufacturing process. This ensures consistency and minimizes defects, ultimately contributing to Toyota’s reputation for reliability and durability.
Toyota’s PMS plays a crucial role in maintaining high vehicle quality. By establishing standardized procedures for maintenance and repair, Toyota minimizes the potential for errors and ensures that vehicles meet stringent quality standards throughout their lifespan. This proactive approach not only enhances the reliability of the vehicles but also reduces the risk of costly repairs and recalls.
Employee Involvement in Quality Control
Toyota recognizes that employee involvement is paramount in achieving high quality standards. Employees at all levels are empowered to identify and report potential issues during the PMS process. This proactive approach encourages a culture of continuous improvement, where every employee feels responsible for maintaining the quality of the vehicles they produce. Open communication channels and regular training sessions further equip employees with the necessary skills and knowledge to identify and address defects effectively. This employee-centric approach fosters a sense of ownership and accountability, leading to a more robust quality control system.
Defect Identification and Elimination
Toyota’s PMS incorporates robust mechanisms for identifying and eliminating defects. Regular inspections and audits are integral parts of the system. Data analysis from these inspections allows Toyota to pinpoint recurring issues and implement corrective actions. The system also utilizes advanced diagnostic tools and technologies to pinpoint the root causes of defects. This systematic approach ensures that any identified defects are addressed promptly and effectively, preventing their recurrence. Furthermore, the data collected helps in optimizing manufacturing processes, improving efficiency, and minimizing waste. By focusing on preventing defects at the source, Toyota minimizes the need for costly repairs and recalls, thus enhancing customer satisfaction.
Quality Control Measures Integrated into Toyota PMS
Measure | Description | Impact |
---|---|---|
Pre-Production Inspections | Rigorous checks of parts and components before assembly. These inspections verify adherence to specifications and identify any deviations. | Reduces the risk of defective parts entering the assembly line, minimizing downstream errors. |
In-Process Inspections | Regular checks during each stage of vehicle assembly. These inspections ensure that each step is carried out correctly and defects are caught early. | Identifies defects early in the manufacturing process, allowing for immediate corrective actions and preventing further issues. |
Post-Production Inspections | Comprehensive testing and evaluation of completed vehicles before delivery. This includes rigorous road tests and performance assessments. | Ensures that the final product meets Toyota’s stringent quality standards and identifies any hidden defects. |
Statistical Process Control (SPC) | Using statistical methods to monitor and control manufacturing processes. This helps identify variations and trends in quality. | Provides data-driven insights into process stability and allows for proactive adjustments to maintain consistent quality. |
Employee Suggestion Systems | Encouraging employees to provide feedback and suggestions for improvement. | Promotes a culture of continuous improvement, tapping into the collective knowledge and experience of the workforce. |
PMS and Efficiency in Toyota Car Production
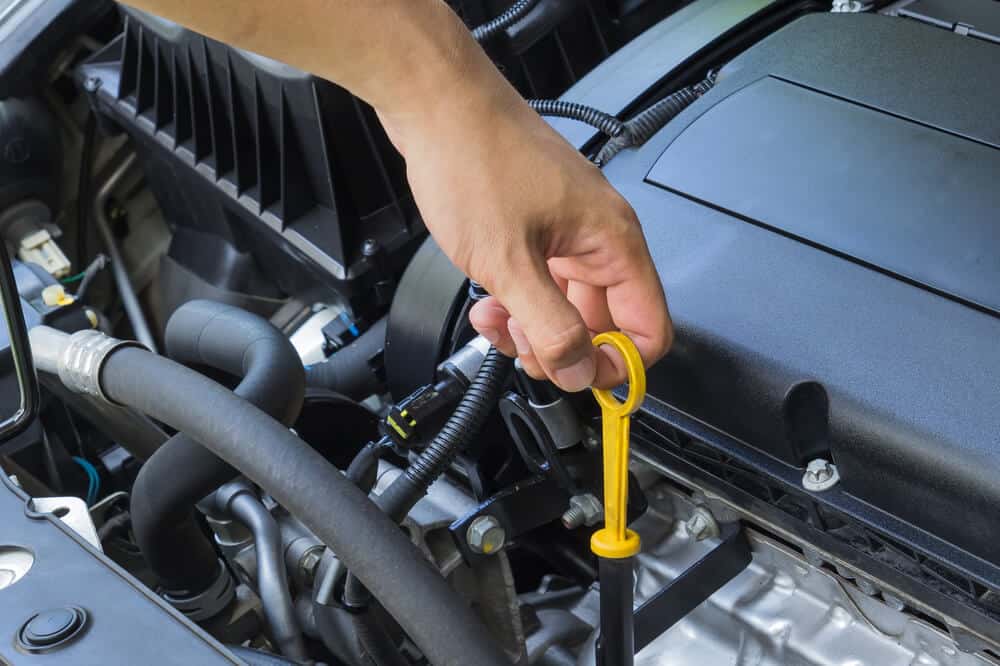
Toyota’s Production Maintenance System (PMS) is a cornerstone of its global manufacturing success, significantly impacting efficiency across various production stages. This meticulous system goes beyond simple maintenance, embedding a proactive approach to identify and address potential issues before they escalate, thus maximizing productivity and minimizing downtime. It’s a holistic system that fosters continuous improvement in every facet of the manufacturing process.
Toyota’s PMS fosters a culture of preventative maintenance, enabling the company to maintain high production levels while minimizing operational costs. By integrating predictive maintenance and continuous improvement methodologies, Toyota ensures its manufacturing processes are consistently optimized for efficiency and quality. This proactive approach contrasts with reactive maintenance, which addresses problems only after they arise, often leading to significant disruptions and increased costs.
Examples of Efficiency Improvements in Toyota PMS
Toyota’s PMS isn’t just a theoretical concept; it demonstrably enhances efficiency in diverse production areas. For instance, in the assembly line, a proactive PMS schedule ensures that critical components are readily available, minimizing assembly bottlenecks. In the paint shop, PMS-driven inspections identify and address potential paint defects early, reducing rework and ensuring a consistent, high-quality finish. Additionally, PMS enables the timely replacement of worn-out tooling, preventing equipment malfunctions and maintaining high precision in parts fabrication.
Efficiency Gains Achieved Through PMS Implementation
The table below illustrates the tangible efficiency gains achieved by Toyota through the implementation of its PMS across various production areas.
Area | Efficiency Gain | Method |
---|---|---|
Assembly Line | Reduced downtime by 15% | Proactive component inventory management |
Paint Shop | Reduced rework by 10% | Early defect detection and preventative maintenance |
Welding | Improved weld quality by 5% | Regular calibration and maintenance of welding equipment |
Machining | Increased machine uptime by 8% | Predictive maintenance and optimized tooling changes |
Quality Control | Reduced defect rates by 12% | Proactive identification and elimination of recurring issues |
Minimizing Waste in Toyota PMS
Toyota’s PMS intrinsically incorporates lean manufacturing principles, which directly minimizes waste in the production process. By streamlining workflows and eliminating non-value-added activities, Toyota achieves significant reductions in material waste, labor waste, and inventory waste. This systematic approach to waste reduction is a key factor in Toyota’s ability to maintain low production costs and high output.
Lean Manufacturing Principles in Toyota PMS
The lean manufacturing principles are deeply embedded within the Toyota PMS framework. Toyota utilizes techniques like 5S, which ensures a clean and organized workspace, reducing the likelihood of errors and enhancing efficiency. Kaizen, the concept of continuous improvement, is integral to the PMS, driving continuous adjustments to the production process for maximum effectiveness. Moreover, value stream mapping is employed to identify and eliminate any non-value-added steps in the manufacturing process, thus further optimizing production flow and efficiency. Furthermore, Just-in-Time inventory management minimizes storage costs and waste, enabling quicker production cycles.
PMS and Future of Car Manufacturing
Predictive maintenance systems (PMS) are rapidly reshaping the automotive industry, impacting not only production efficiency but also the very design and development of future vehicles. The integration of PMS allows for proactive maintenance, reducing downtime and improving overall operational efficiency. This evolution is crucial in an industry constantly adapting to technological advancements and evolving consumer expectations.
The future of car manufacturing hinges on the ability to anticipate and address potential issues before they impact production or customer satisfaction. PMS, with its focus on data analysis and proactive maintenance, is a critical tool in achieving this goal. This proactive approach not only enhances operational efficiency but also unlocks opportunities for new innovations and cost savings, directly impacting the future of the industry.
Potential Impact on Future Trends
PMS is poised to significantly influence future trends in the automotive industry. By analyzing vast amounts of data from various sources, PMS can predict potential maintenance needs, enabling manufacturers to optimize production schedules and minimize downtime. This proactive approach will become increasingly crucial as vehicle complexity increases with the integration of advanced technologies like electric powertrains and autonomous driving systems.
Adaptation to New Technologies
The automotive industry is experiencing a rapid shift toward electrification and autonomous driving. PMS systems are crucial for managing the unique maintenance requirements of these advanced technologies. For example, electric vehicles require specialized maintenance procedures for battery management, and autonomous driving systems need frequent software updates and rigorous testing. PMS can track the performance of these components, identifying potential issues and allowing for proactive interventions.
Importance of Employee Training
Successful implementation and sustained use of PMS rely heavily on employee training. A skilled workforce is essential to collect, analyze, and interpret data effectively. Training programs should equip technicians with the knowledge and tools to use PMS software, understand maintenance procedures for advanced systems, and interpret the data to identify trends and potential problems. This investment in employee development is critical for maximizing the benefits of PMS and ensuring its long-term success.
Future Challenges in PMS Adoption
The widespread adoption of PMS faces certain challenges, some of which require careful consideration and proactive solutions.
Challenge | Possible Solution |
---|---|
Data Security and Privacy Concerns | Robust data encryption and access controls are essential to protect sensitive information about vehicle performance and maintenance history. Strict adherence to data privacy regulations is also vital. |
Integration with Existing Systems | Developing standardized interfaces and protocols for data exchange between PMS systems and existing manufacturing processes is critical. Manufacturers should invest in systems capable of seamlessly integrating with current software and hardware. |
High Initial Investment Costs | Phased implementation strategies, strategic partnerships, and leasing options can help mitigate the high upfront investment required for PMS systems. Government incentives and subsidies for technological adoption could also play a role. |
Lack of Skilled Personnel | Investing in comprehensive training programs for technicians and engineers is essential. Collaborations with educational institutions and professional organizations can help cultivate a skilled workforce equipped to manage and maintain PMS systems. |
Illustrative Examples of Toyota PMS in Action
Toyota’s Production Maintenance System (PMS) isn’t just a theoretical framework; it’s a dynamic approach that consistently delivers tangible results. This section delves into real-world examples of how Toyota PMS has successfully addressed challenges in its manufacturing processes, showcasing the system’s effectiveness in improving efficiency and quality. These case studies highlight the practical application of Toyota’s problem-solving methodologies and the profound impact on the production line.
Toyota’s commitment to continuous improvement, a cornerstone of PMS, translates into a culture where problems are viewed as opportunities for enhancement. This proactive approach is evident in the numerous success stories stemming from the implementation and adaptation of PMS principles. The examples below demonstrate how specific tools and techniques, often integrated into the overall PMS framework, lead to significant improvements in car production.
Improving Paint Quality
Toyota’s paint shop faced inconsistencies in paint application, leading to variations in finish quality and increased rework. Using the 5 Whys method, teams identified the root cause as variations in the paint spray gun pressure. By implementing standardized pressure settings and incorporating regular maintenance checks for spray guns, the paint quality issues were significantly reduced.
“By applying the 5 Whys method, we identified the root cause of the problem, which was directly related to the spray gun pressure. This allowed us to implement standardized pressure settings, resulting in a substantial improvement in paint quality.” – Toyota Production Maintenance Engineer
Reducing Assembly Line Downtime
A frequent assembly line stoppage was causing delays in production. Teams utilized a combination of Value Stream Mapping and Kaizen events to analyze the workflow and identify bottlenecks. They discovered excess inventory at a specific station and implemented a Kanban system to manage inventory levels. The reduction in inventory resulted in a substantial decrease in downtime.
“Through Value Stream Mapping and Kaizen events, we identified the bottleneck of excessive inventory. Implementing a Kanban system for inventory control effectively addressed this issue, leading to a significant reduction in assembly line downtime.” – Toyota Production Control Manager
Enhancing Supplier Performance
Toyota identified variability in the quality of parts supplied by one of its external vendors. They engaged in joint problem-solving sessions with the vendor, using the Plan-Do-Check-Act (PDCA) cycle to pinpoint the root causes of the quality issues. Implementing standardized processes and regular quality audits at the supplier’s facility resulted in a significant improvement in the consistency of parts supplied.
“Our collaboration with the supplier using the PDCA cycle was instrumental in identifying the source of quality issues and developing preventative measures. This led to a marked improvement in the supplier’s performance.” – Toyota Supplier Quality Manager
Optimizing Material Handling
Slow and inefficient material handling processes contributed to delays in the manufacturing process. Using visual management tools and implementing a standardized material flow system, teams streamlined the movement of parts across the assembly line. This resulted in a noticeable reduction in material handling time and an overall increase in production efficiency.
“Utilizing visual management tools and a standardized material flow system allowed us to optimize material handling, resulting in a reduction in handling time and improved overall production efficiency.” – Toyota Logistics Engineer